MARKET: PLASTIGAUR INSTALLS INLINE MDO RETROFIT TO PRODUCE PET-REPLACEMENT FILM MADE FROM ORIENTED PE
The claim of PLASTIGAUR, a manufacturer of flexible packaging located in the north of Spain near San Sebastian, is “Innovation is Flexible”. So, it’s no wonder that PLASTIGAUR has set high goals for itself regarding sustainability. The company aims to have all of their packaging be 100% recyclable by 2022. With today’s PET/PE laminates (e.g. for stand-up pouches, flow-pack), this would not be possible. This led PLASTIGAUR to explore alternative manufacturing options. The inline MDO process was identified as the best solution for replacing PET with oriented PE (OPE) to create a recyclable laminate. Together with W&H as PLASTIGAUR´s supplier of their last two blown film lines, a new project for an inline MDO was started.
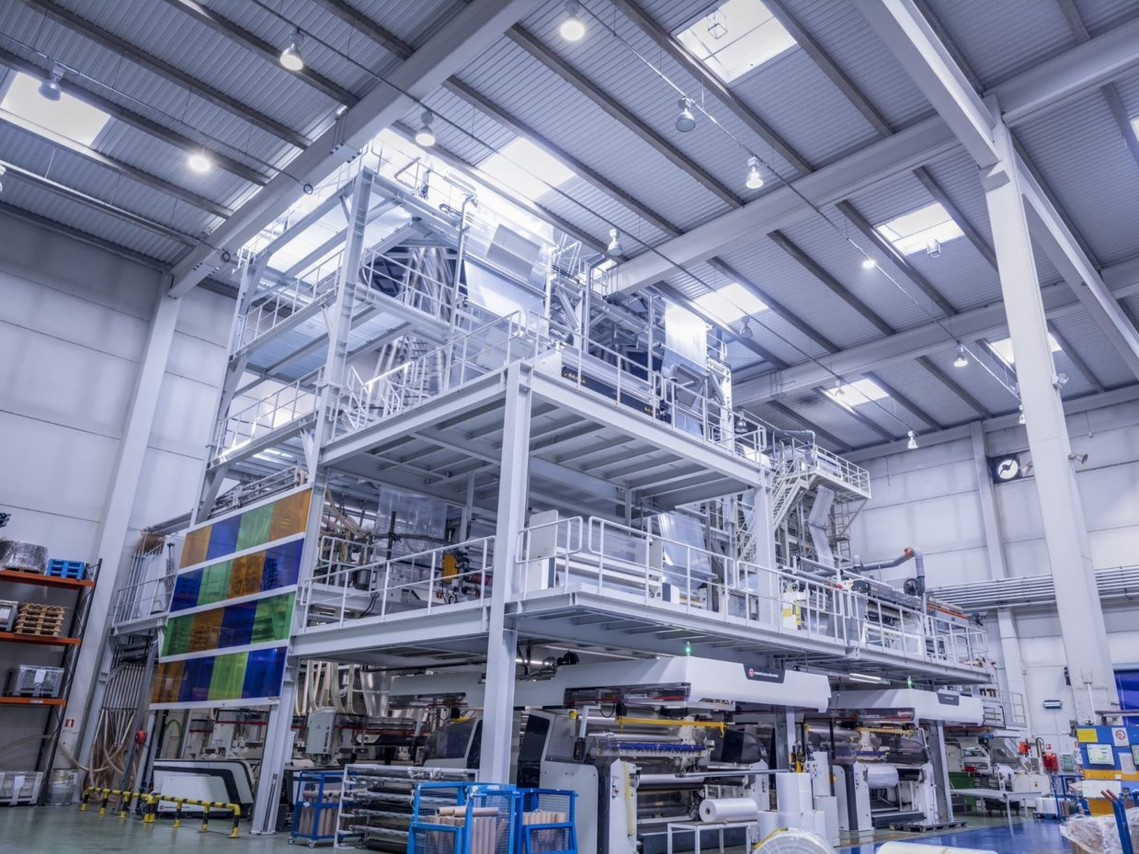
Original configuration
Defining the project: New machine or retrofit
The first decision to make was either to install a completely new line OR to retrofit the MDO technology to one of the existing lines. The modularity of the W&H equipment allows to retrofit all necessary components without compromising the performance in comparison to a completely new installation. After evaluating all options together with the trusted technical consultants from W&H it was decided to retrofit an existing 5 layer VAREX II machine, which already has served PLASTIGAUR over the last 5 years producing conventional PE films.
Getting started: Fitting the new equipment into the existing structure
The extrusion building had enough space to extend the existing tower structure to accept the additional equipment like the TCUs, gauge measurement and the MDO itself in the area above the winder platform of the second machine. However, such type of retrofit is a major job that requires professional planning and control throughout the whole process.
At first the steelwork for additional platforms above the winder were installed before placing the new components into the machine. Everything was tight, but with suitable rigging equipment and skilled workers on site, who cleverly pre-planned the installation sequence, everything worked out. The pandemic in 2020 was an additional challenge, but the availability and professional support of W&H service technicians based in Spain paired with the perfect support of the team of PLASTIGAUR ensured that an on-time delivery and installation despite the COVID-19 situation was achieved.
Pre-marketing product production and training via video
Parallel to the installation of the machine components, PLASTIGAUR and W&H worked on pre-marketing activities producing first sample rolls as well as a training program. However, travel restrictions wiped out the original plan and a new strategy was needed. In the end PLASTIGAUR provided the raw materials and the W&H lab team conducted the trials with PLASTIGAURS experts joining from the distance. But how does that work?
Using video-conferencing tool combined with mobile cameras moving through the machine and access to the machine operating panel W&H provided a useful documentation of the trials and sample roll production. From the distance PLASTIGAUR was able to dive through all operating and data pages of the running machine at the W&H technical center as if they operated the machine themselves!
Start of production: 100% as expected
After all systems got installed and checked out, the first footage of oriented PE films was produced. This new product requires an elaborate recipe as well as matching parameter setting for the equipment. The result: rolls of high performing film that run through the printing and lamination process at high speeds and with low waste rates.
This project shows that partnership between a trusted and capable machine supplier and an innovative thinking producer of flexible packaging with dedicated staff leads to a successful jump-start, even for a challenging new product like the PET-replacement film made from oriented PE.
This addition of OPE film production capacity underlines PLASTIGAUR´s commitment for sustainability in flexible packaging. W&H as their trusted machine supplier had the chance to demonstrate what can be achieved despite COVID-19 restrictions and delivered 100% as expected.
Interested in a consultation to retrofit your machines?
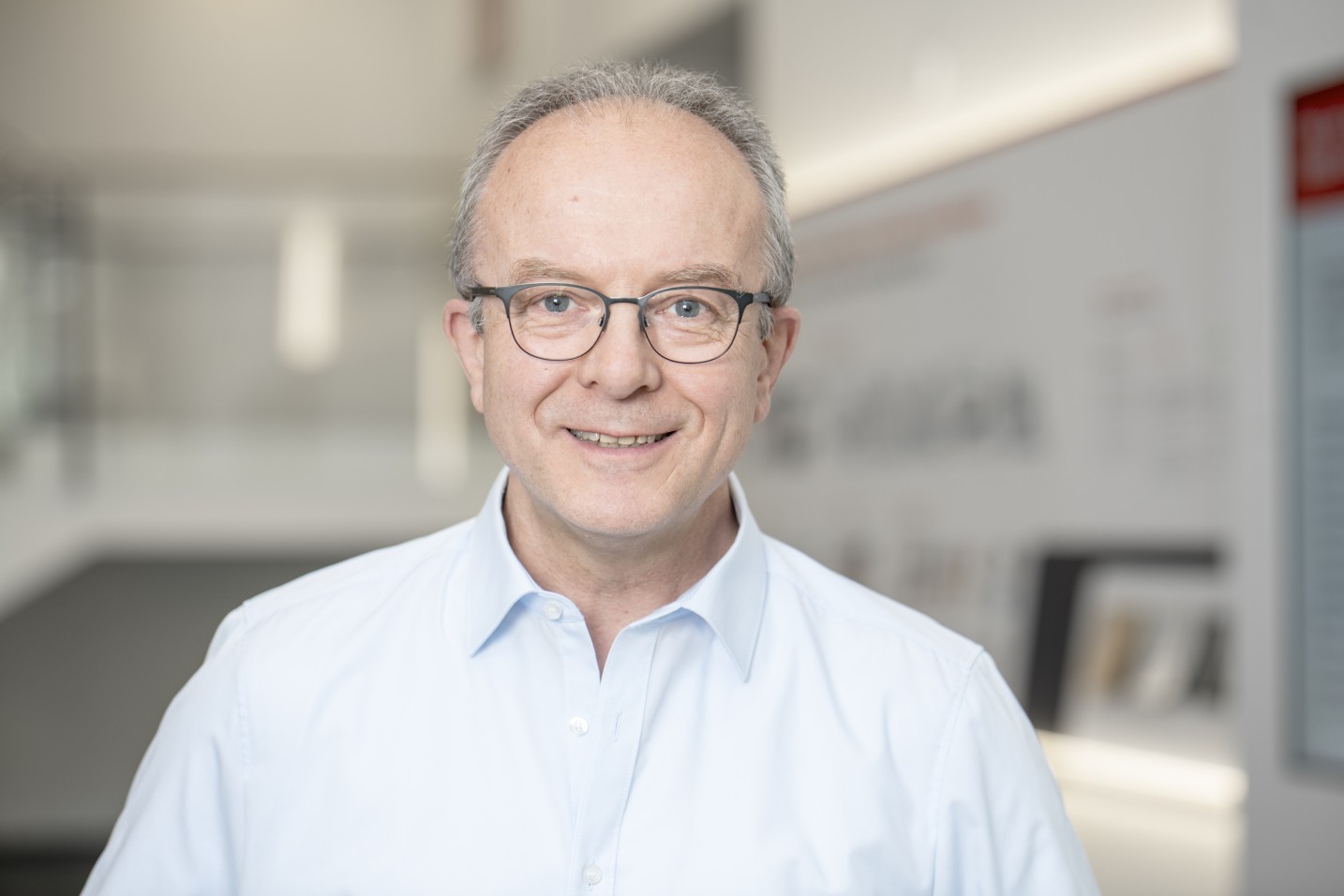
Gerd Kasselmann
Regional Manager Technical Sales Business Unit Extrusion