Refreshing a 20-year-old ASTRAFLEX
Extend press life, ensure parts availability, and improve print quality with a strategic upgrade
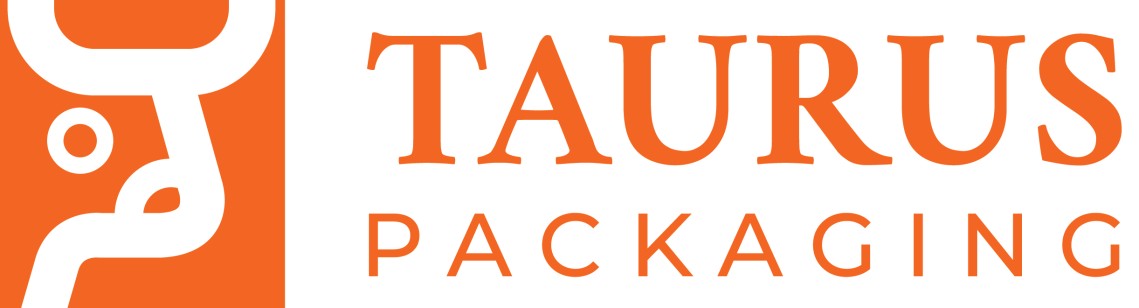
Taurus Packaging
Taurus Packaging was established in 1977 as a manufacturer of potato sacks in Cape Town. In 1979, the company relocated its factory to Northern KwaZulu-Natal to be closer to key sack market customers and leading paper suppliers. Since then, Taurus Packaging has continuously expanded and is now one of the leading paper bag manufacturers in South Africa. The company serves all segments of paper bag and sack users in the country, with the capacity to annually convert over 28,000 tons of paper into high-quality printed bags.
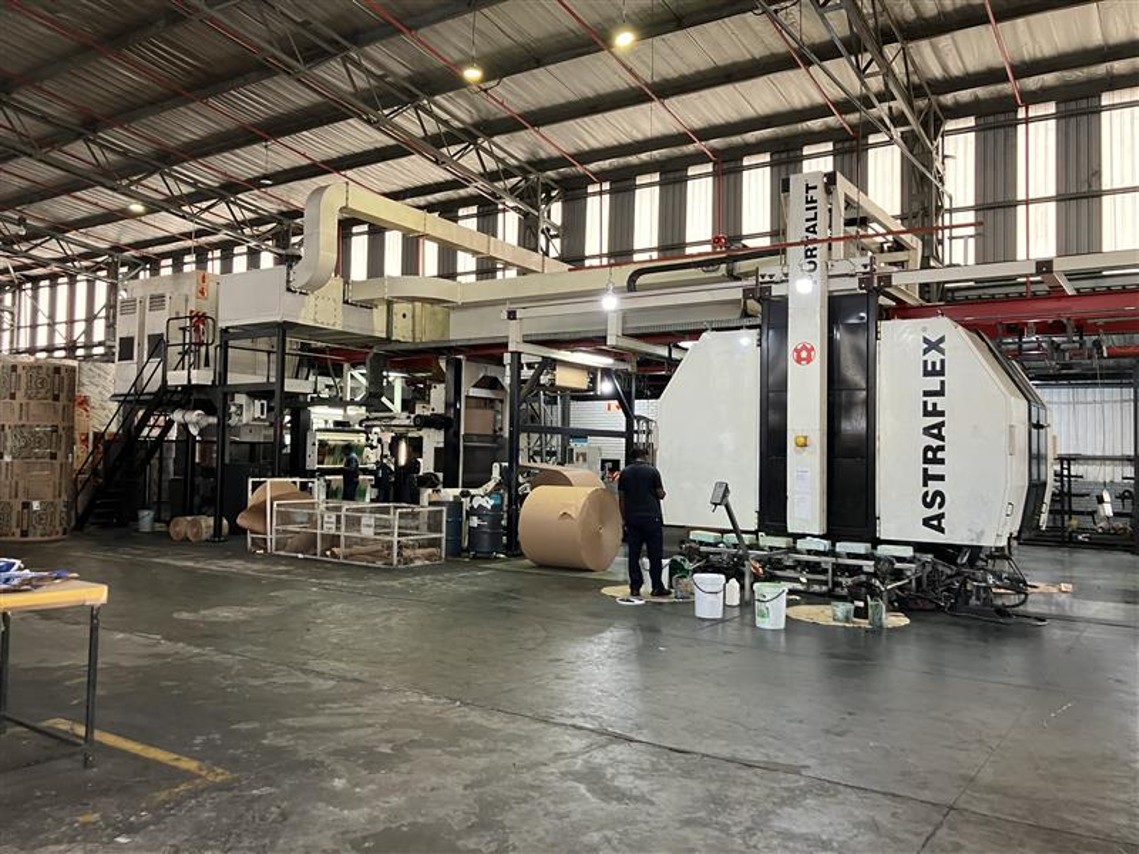
State-of-the-art again after retrofit measures: the 20 year old ASTRAFLEX printing press from W&H.
Investing in the future
Taurus Packaging has great confidence in the quality and reliability of Windmöller & Hölscher (W&H) machines, which form a significant part of its machinery. This includes several W&H converting machines, equipment from the W&H subsidiary Garant, and two W&H printing presses: a MIRAFLEX C and an ASTRAFLEX .The ASTRAFLEX flexo press in particular has been in operation for over 20 years, demonstrating outstanding reliability and minimal maintenance costs throughout its life cycle. However, it was time to bring the machine up to date. This upgrade would ensure the future availability of spare parts and further extend the life of the machine, enabling Taurus Packaging to maintain its highstandards of quality and efficiency for years to come.
A comprehensive retrofit for continued excellence
The retrofit included a comprehensive replacement of obsolete components in key areas of the ASTRAFLEX. Upgrades included new color deck adjustment motors and frequency converters on the printing stations, as well as updated control units and computers for the unwind, rewind, drying unit, main drive, and anilox. Additionally, the Portalift received an electrical upgrade. To further modernize operations, a new main computer with touchscreen capability and updated I/O modules were installed, integrating the latest hardware and software.
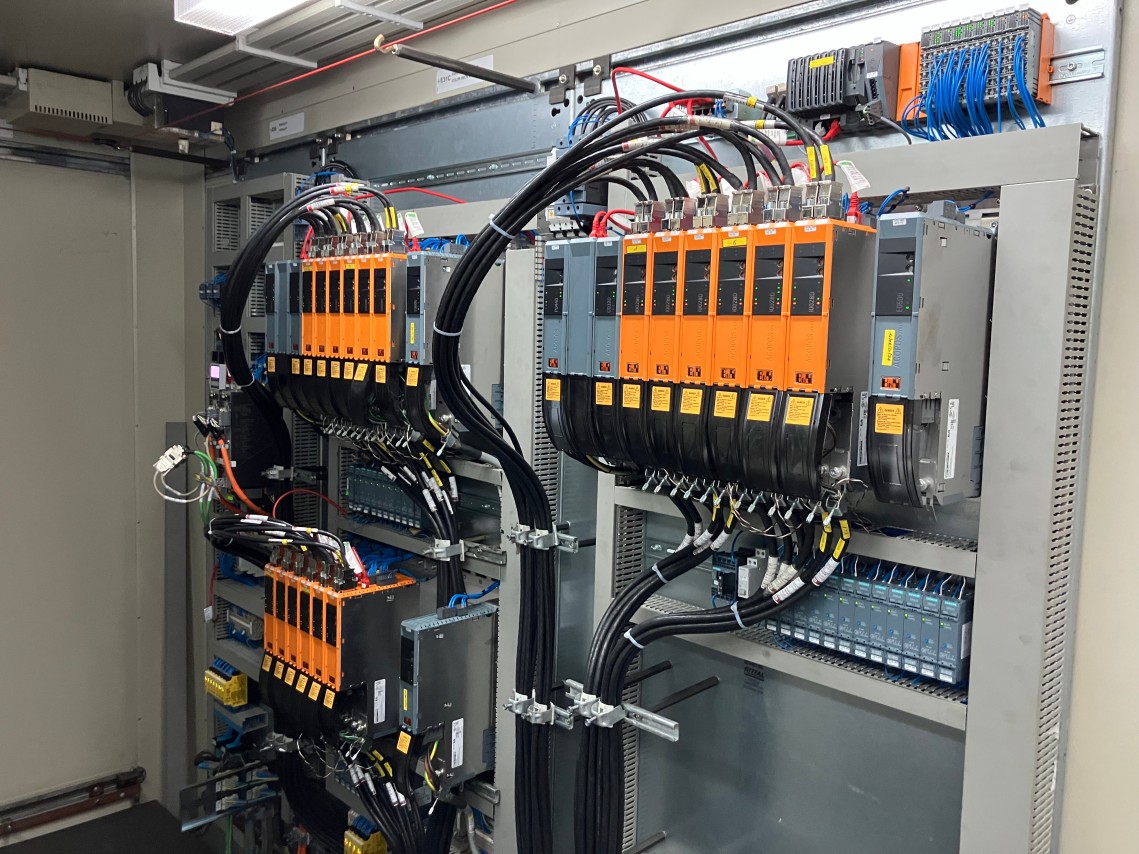
The latest electrical components have been integrated to ensure a system that is future-proof.
A great success
By retrofitting the ASTRAFLEX with state-of-the-art components, the printing press not only became more user-friendly but also saw a significant increase in efficiency. Over the course of seven weeks, W&H technicians worked closely with the Taurus team to complete these upgrades with minimal disruption to operations and to ensure that the installation met the customer‘s expectations. With daily feedback and a well-defined plan, the project was completed successfully and on time. The results of the retrofit exceeded all expectations: production output increased by 30% and print quality improved thanks to the new, precise technology.
A satisfied customer: Taurus Packaging already plans the next step
Taurus Packaging is fully satisfied with the retrofit and has already agreed to a further retrofit on one of their existing complex W&H lines. The dedication and support of the W&H team has been instrumental in overcoming all challenges - even going beyond the original scope to assist with issues on other machines. With this successful project, Taurus Packaging has laid a strong foundation for a sustainable and productive future.