PURE Flexible Packaging Seminars
From January 14 to 21, W&H hosted a seminar roadshow in Jakarta, Bangkok, and Manila. Over 500 participants attended, engaging with the latest trends, updates, and innovations in the flexible packaging industry.
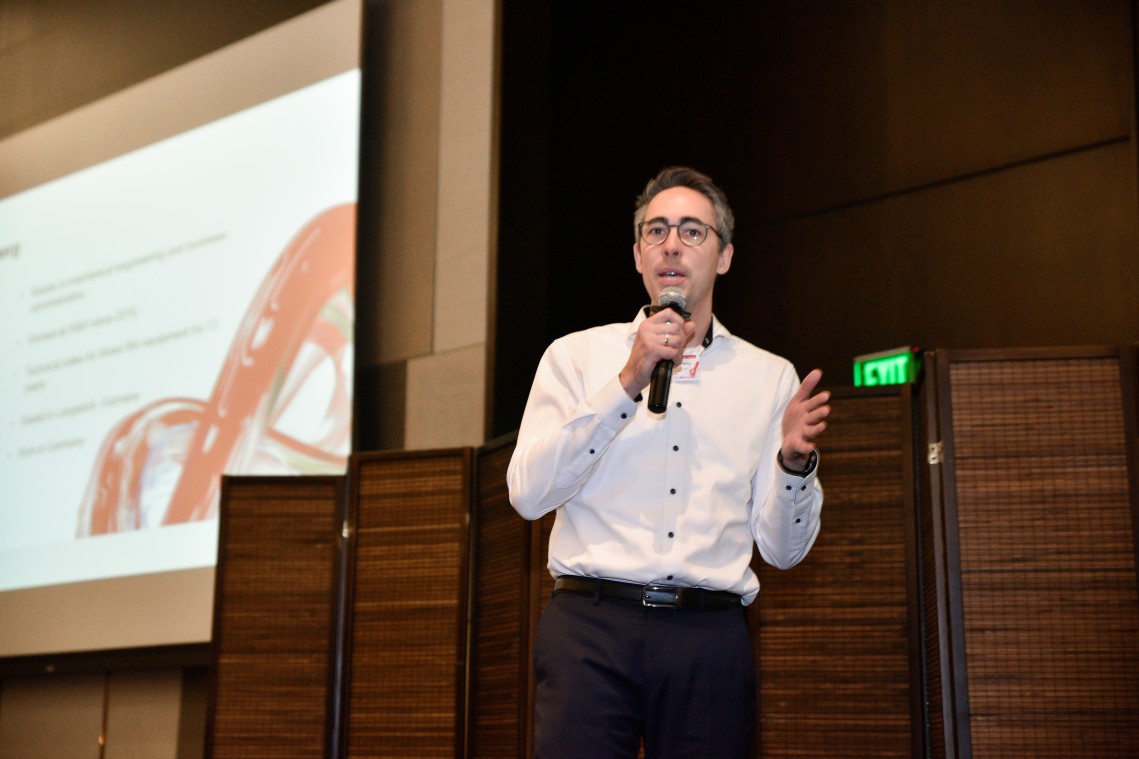
Besides presentations from W&H experts about the latest trends and innovations in extrusion, printing and sustainability, the roadshow featured contributions from our subsidiaries and key industry partners. GARANT presented paper-bag making solutions, while our partner B&B Verpackungstechnik showed the pouch and bag making solutions for mono-materials and large bags. Nordmeccanica, a partner of W&H Asia Pacific, highlighted the latest developments in sustainable laminations. A special highlight was the recent distribution agreement between Kampf-Atlas, a global leader in slitting equipment, and W&H Asia Pacific. The roadshow provided an excellent platform for Kampf-Atlas to introduce their solutions to a wide audience across the three seminar locations.
In between the presentations, all participants mingled in a relaxed atmosphere while enjoying good food and drinks.
The customer feedback was overwhelmingly positive. Just two days after the final seminar, the roadshow ended on a high note with a handshake sealing the deal for a new Alphaflex CI press from one of our customers.
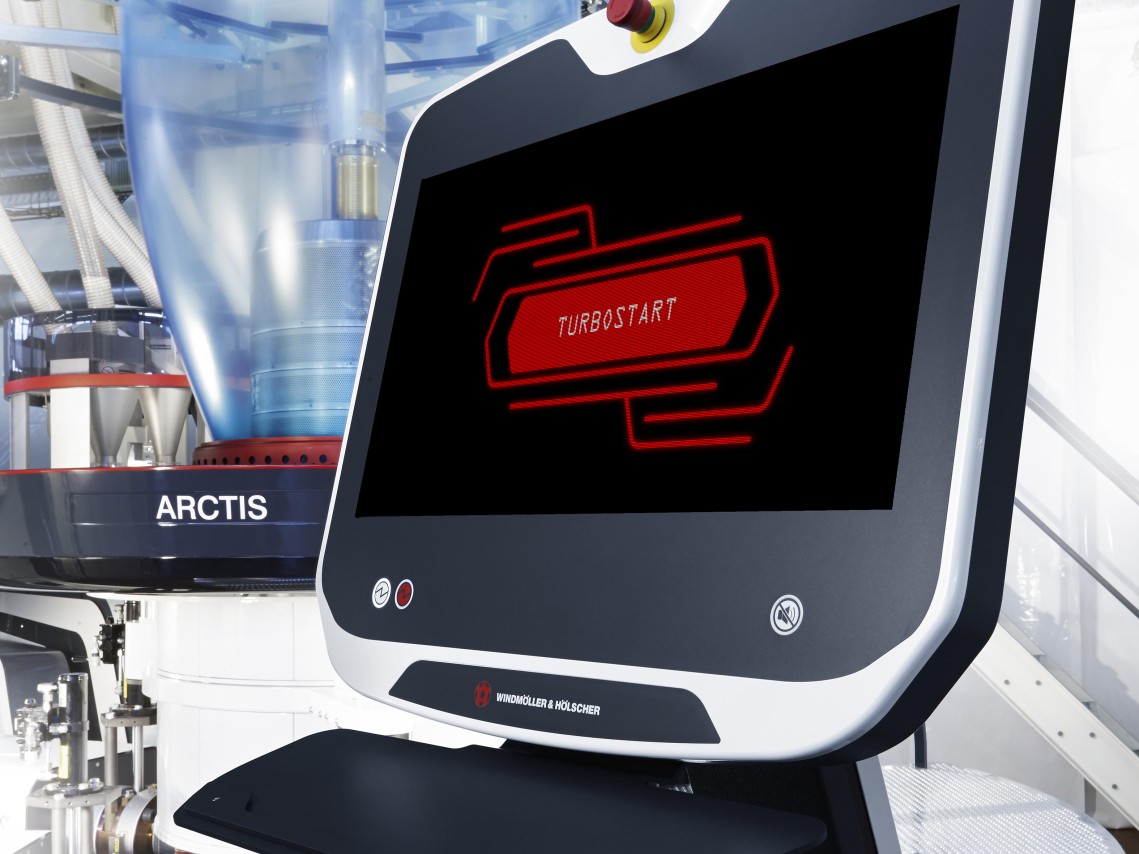
Presented Topics - Extrusion
So far, PET/PE Duplex, Triplex- and other multi-layer laminates with different chemical characteristics have been the market standard. Unfortunately, when materials have different chemical characteristics, recycling is difficult. The solution is either working with mono-materials or with lamination layers that are chemically uniform within certain guidelines. One example is MDO-PE film - Machine Direction Oriented - PE film. This is a type of film that is 100% recyclable and environmentally friendly. It is made using a special processing technique that involves stretching PE films in the direction it is being produced. This process improves the film's properties and makes it suitable for making pouches using PE only. Therefore, it is good for recycling. W&H has tested MDO-PE film-based pouches with different types of barrier coatings and films. There is a solution for mono-material packaging for almost every type of application. From food to chemicals.
Using recycled plastics is another way to contribute to a sustainable environment. Collecting used plastics and converting these into resins for making films is already used in many applications. For example, bags for industrial packing and secondary packing like stretch films. More and more applications are coming to the market. W&H plays an important role in the development of the use of recycled materials.
Reducing waste during the production of film and lower energy cost are other areas where W&H is launching solutions. For example, the TURBOSTART function for extrusion lines reduces the many steps for the machine set-up to just seven buttons on one screen. Saving a lot of time and film waste in the process. New camera technology acts as the digital eye of the blown film operator. Enabling consistent film quality without the need of years and years of operational experience.
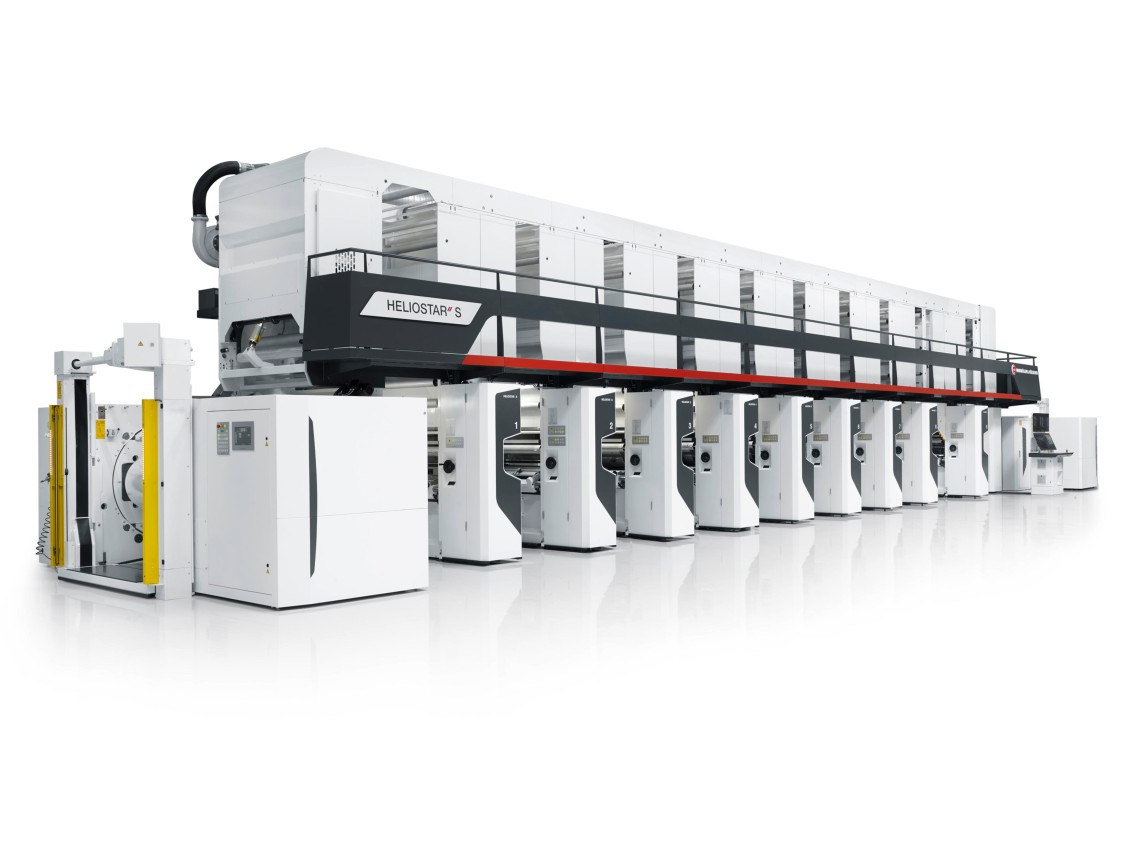
Printing
Producing recycled materials is one thing. But what about printing it? Making pouches with resins made of recycled materials (PCR) has some negative effects on the way the film behaves in the web printing machines. You can have issues with repeat tolerances, web shifts, web breaks and/or creases. By continuous measurement of the actual print repeat length under tension conditions and dynamic repeat length corrections during production, the W&H CI flexographic press range and the HELIOSTAR gravure presses ensure a perfect register. Even during ramping up and ramping down or at full production speed.
Printing barrier coatings benefits recyclability. Pouches made of laminates of one material, like MDO-PE and LLDPE, with barrier coatings can have the required barrier functions for many applications. Even though the cost of barrier coatings is estimated to be slightly higher compared to PET/PE barriers, they are easy to master and quickly to implement. No primer needs to be printed.
Barrier coatings are not for all applications though. There is no one best solution. All solutions have advantages and disadvantages. Depending on the individual application.
One technology that has been in the spotlight for many years is digital printing. A technology that has completely taken over the commercial print world, the sign & display world and is making further inroads in label printing and even our flexible packaging world. In flexible packing the adoption has been relatively slow. Some main reasons are that we are working with many different substrates, high coverage of e.g. white inks and often with food related packaging. A digital machine for this is quite different from the digital presses that we are seeing in the commercial print and label print business. W&H has created the solution. A digital hybrid press that fits into our flexible packaging world. The digital press that W&H is developing was demonstrated at his premises in Lengerich, Germany during the period of the DRUPA exhibition.
70 years ago, W&H invented the central impression technology. This technology characterizes modern flexographic printing today. The base of W&H’s digital press is a central impression cylinder. This technology characterizes high quality flexographic printing with excellent register accuracy even with the most challenging substrates. W&H’s digital printing machine can be equipped with up to 7 inkjet printing units located above the central impression cylinder, supported by 4 flexographic printing decks for processing lacquers, white or other inks, which are usually used within the flexible packaging industry.
This enables production in Expanded Color Gamut mode and the achievement of almost all Pantone spot colors. The addition of four flexographic printing units makes it possible to print on a wide range of substrates, print many applications with substantial cost benefits. This high-performance press can reach a very high maximum speed of up to 150m/min. So, please stay tuned for the launch of W&H’s digital press.
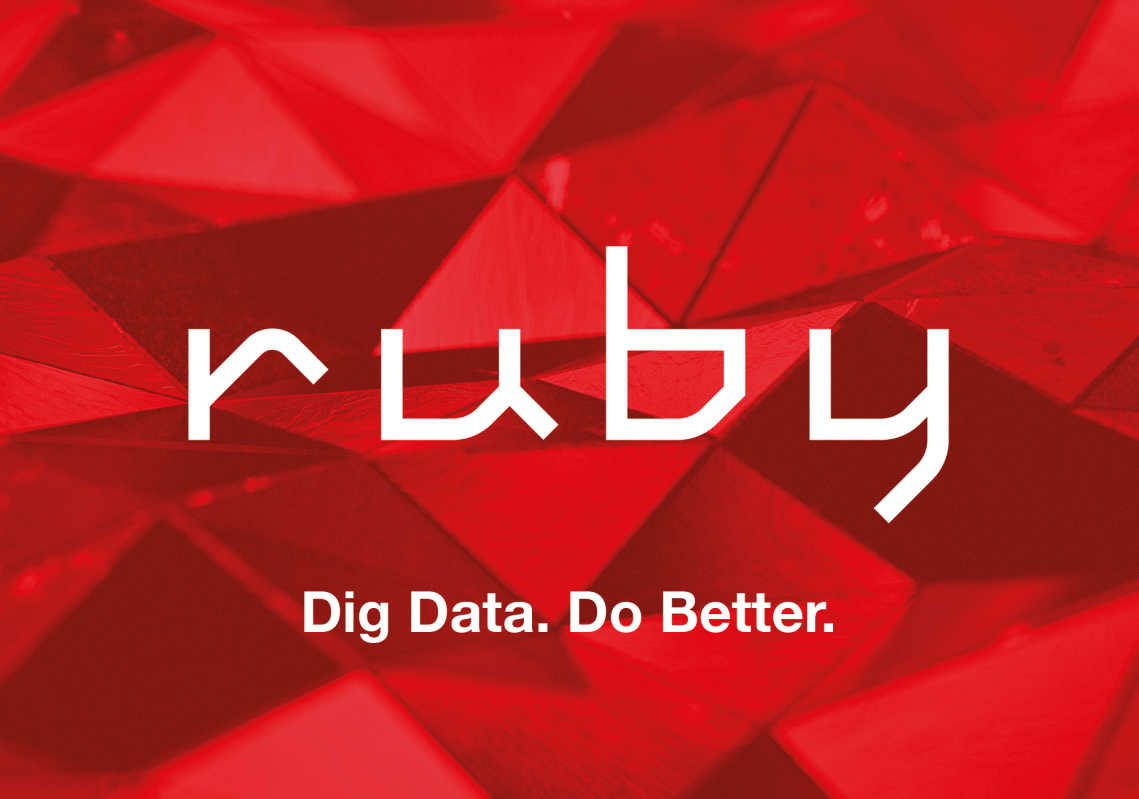
The Power of using Big Data
One technology that is extraordinarily powerful is sensor technology. IoT, the use of data from your equipment. We are seeing sensor technology everywhere around us these days. In our cars, at home, in planes, in the medical industry, etc. It is the 4th industrial revolution. It is affecting our flexible packaging industry as well. The use of factual data makes our production world transparent. No need to guess. We can look at facts by using real data to decide on operation improvements. In today’s world, digital transformation isn’t just an option. It’s an essential step for staying competitive. Statistics show that while 90% of companies recognize its importance, 80% are still in the early stages of implementation. Why? Perceived barriers like complexity of implementation, integration in existing set up, cost and steep learning curves often hold them back.
The connectivity system of W&H - RUBY – makes the implementation easier. RUBY offers flexible, scalable solutions and enables you to start small, grow the use of connectivity and data at your own pace.
Converting - Our Partners
W&H Asia Pacific has for years a distribution agreement with the advanced bag and pouch making machine manufacturer B&B Verpackungstechnik.
In 2024, W&H Asia signed a distribution agreement for South Korea, Taiwan, Thailand and the Philippines with the market leader in lamination equipment Nordmeccanica, Italy.
Early this year, W&H Asia Pacific and the market-leading slitting machine manufacturer Kampf-Atlas signed a distribution agreement for Indonesia, Vietnam, Philippines and Thailand.
The paper-bag making machine manufacturer GARANT Machinery is a subsidiary of W&H and contributes to the sustainable packaging solutions, as only paper substrates are converted to e-commerce-, shopping- flat-and satchel- and/or SOS bags.
Further, W&H makes a series of equipment for the production of multiwall paper sacks. So, W&H Asia Pacific is very well positioned to advise objectively on a wide range of converting solutions for the flexible packaging.
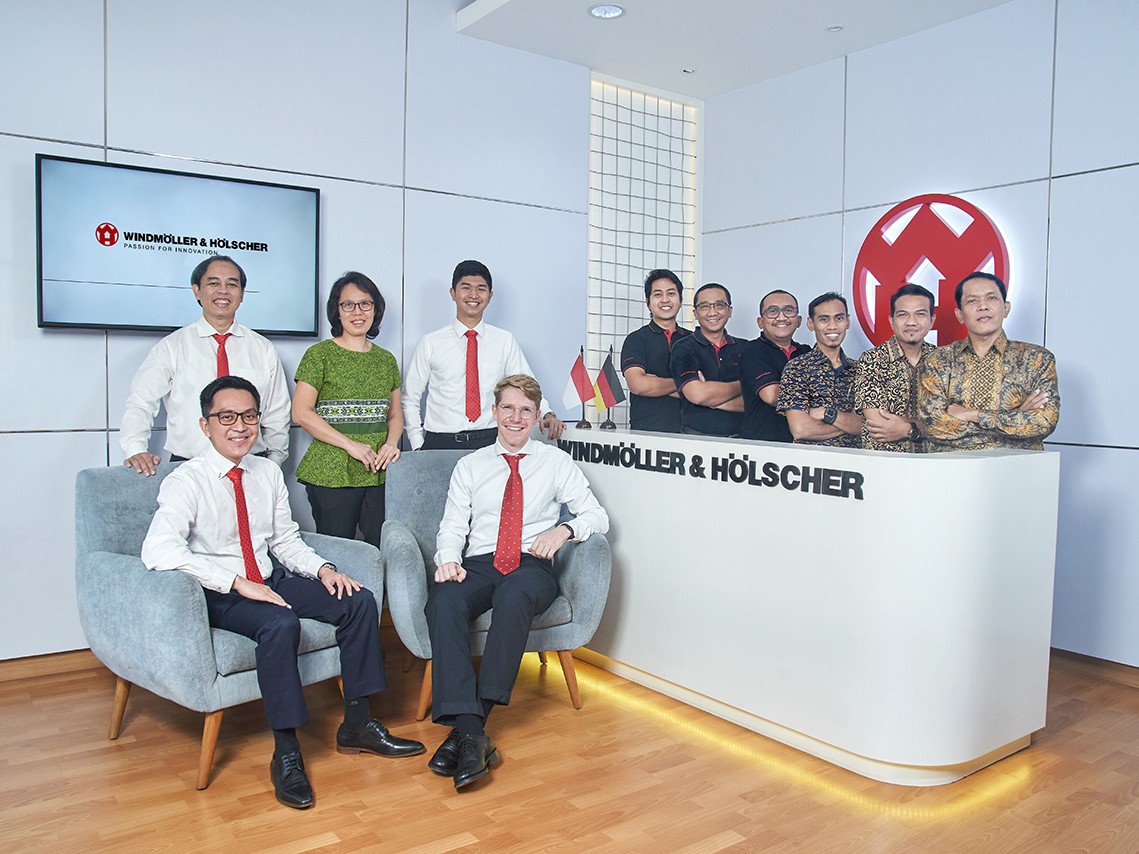
W&H Asia Pacific – a very strong service support organization
With 180 people in Asia (excluding the India region) of which 70 engineers and 40 service support staff, W&H’s Asia Pacific hub in Bangkok, Thailand has a very strong presence in Asia with 11 entities. Not only for new equipment, but also to get more out of existing machines. A range of upgrades and retrofits are available to boost the output, speed or performance of existing machines. This combined with production support and a complete program of trainings.