Increased efficiency with VISION retrofit
Implementation of advanced inspection and automation system to boost production quality and reliability.
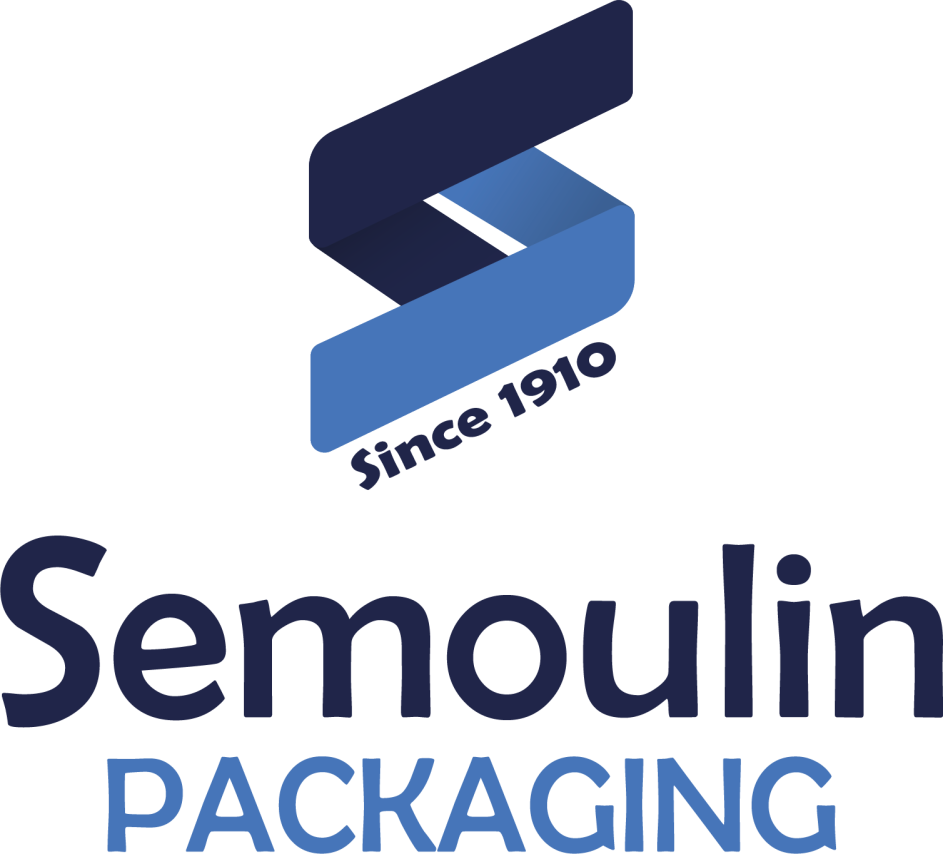
Semoulin Packaging - a long-term W&H customer
Semoulin Packaging, a Belgian company in Hainaut, specializes in paper bags and printed reels. Founded in 1910, this family-owned business combines over a century of experience with continuous production modernization to ensure quality and service.
Semoulin has relied on machines from W&H and its subsidiary Garant in its production for many years and was very pleased with the performance of the VISION inspection and automation system on one of their flexo printing presses.
VISION - for increased production efficiency
The VISION System offers intuitive operation with a unified control for both press and inspection, ensuring faster and more reliable job setups. It provides intelligent inspection and analysis through direct information flow between press functions and inspection data, allowing for advanced root cause analysis of print defects. Focused on customer needs, it includes a wide range of modules like BARCODE CHECK and PDF CHECK, with continuous development based on user requirements. W&H’s renowned service guarantees quick response and expert support worldwide.
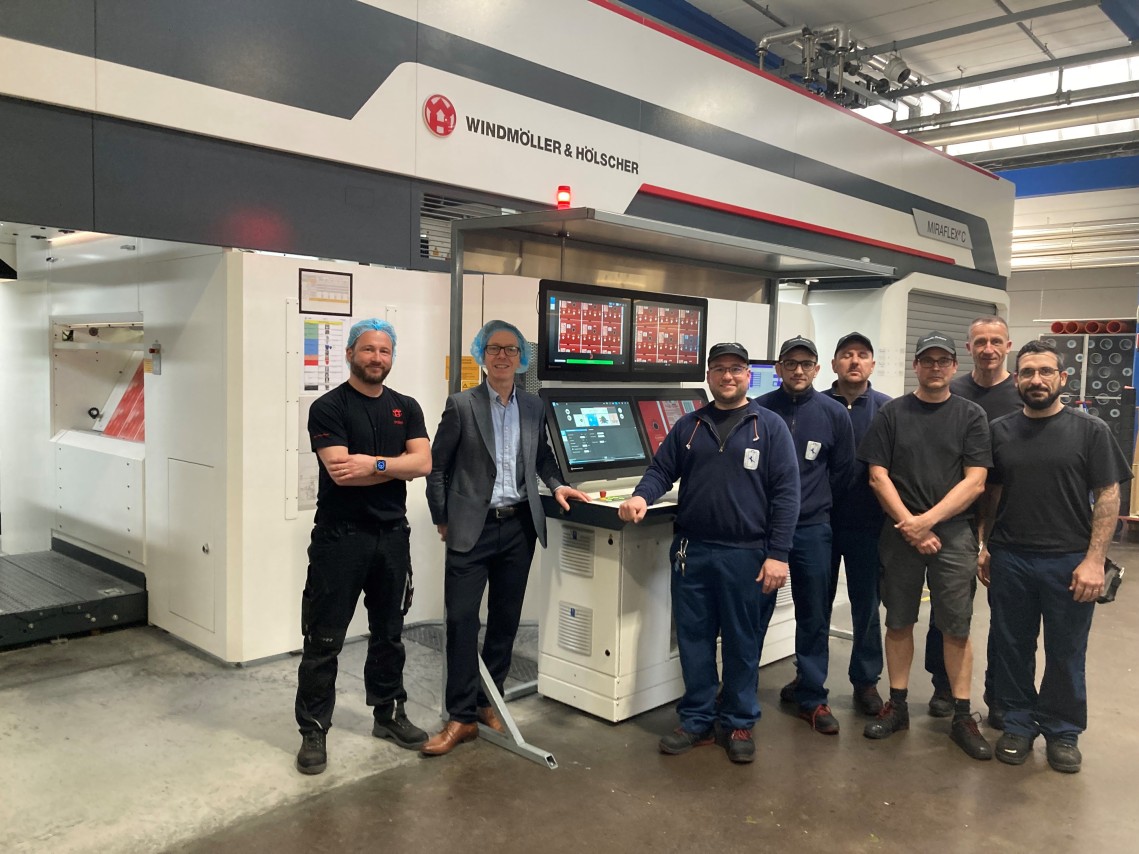
Decision for VISION retrofit
The Semoulin team was eager to work with VISION and wanted to use this tool on an older flexo printing press as well. Loris Piscedda, Maintenance Manager at Semoulin, states, „We already had good experiences with the W&H team in the past, so installation and startup was realised in a fast and efficient way. Interaction with our maintenance team was excellent, the follow-up on open points was managed quite well and we particularly like the support from IDC that helps to solve any hickups instantly.” In just under two weeks, the older MIRAFLEX was retrofitted and the integrated web monitoring and error detection system VISION was installed.
Mathieu Dehon, Production Manager at Semoulin, explains the motivation behind the retrofit: „First of all, the system is performing better than other systems we are familiar with. It is a very intuitive system, easy to handle for the operators and we clearly see the advantage of one provider offering a completely integrated system. That is why we decided to have a standardised way of working on both machines and go for a retrofit. We wanted to have an automatic impression and register setting EASYSET and EASYREG HD on our first machine as well, to have faster and more consistent job changes.“
Satisfied customer and more to come
“We are very pleased with the results. We look forward to continuing our collaboration and the implementation of other interesting retrofit solutions that bring added value to our production process.” concludes Mathieu Dehon.