Retrofit Solutions for W&H Printing Presses
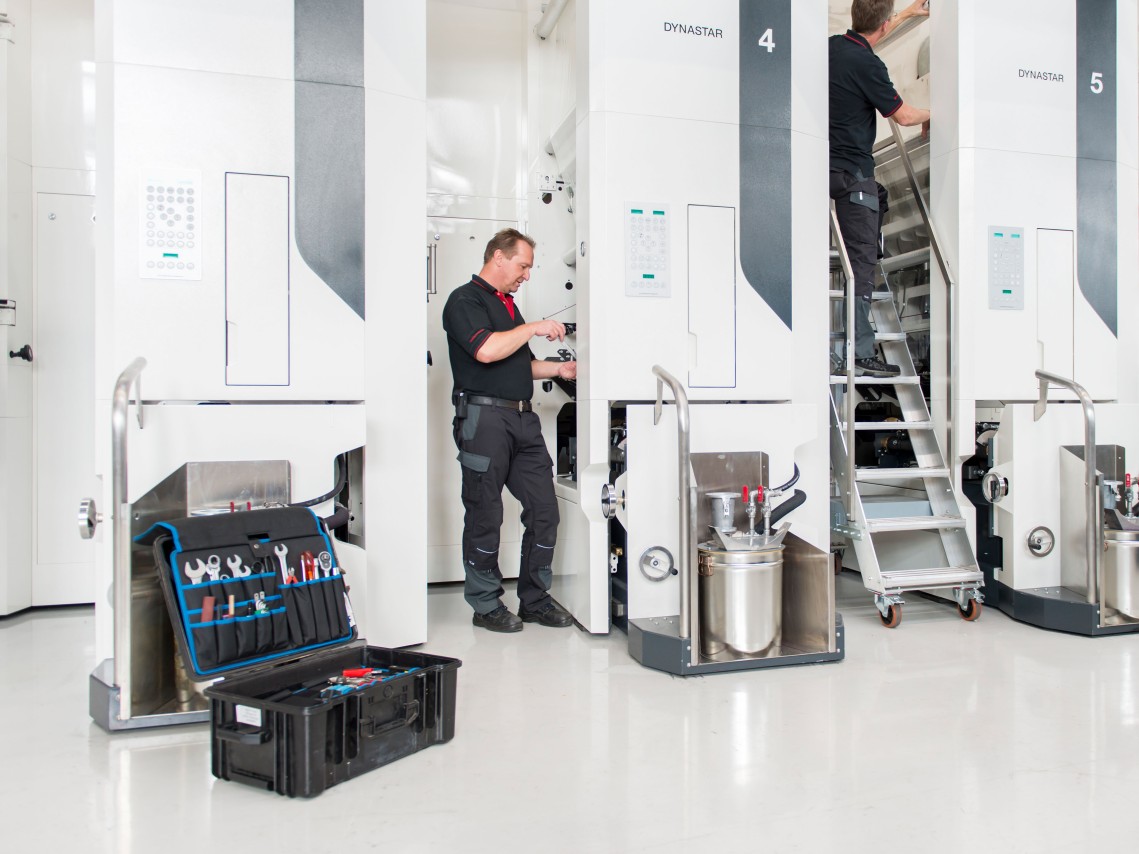
High efficiency, top quality and maximum flexibility at low prices - the market demands highest performance from flexible packaging manufacturers. However, investing in new machinery is not always the best solution to meet these requirements. With our retrofit solutions, new functions or modules can be added to existing printing presses. The development of customer-specific special solutions is also one of our core competencies. This enables you to react to new challenges at any time.
Our retrofit solutions address individual needs, such as:
- Quality improvement & monitoring
- Industry 4.0
- Process engineering
- Energy saving
- Cost reduction
- Operator friendliness
- Performance increase
- Occupational safety
CHOOSE FROM DIFFERENT RETROFIT SOLUTIONS FOR YOUR PRINTING MACHINE
Energy Monitoring
Printing presses consume large amounts of energy in form of electricity, heat (gas, thermo-oil, etc), compressed air and chill water.
Annual energy consumption can be tracked easily but it is difficult to track the actual consumption per print job.
INSTALLATION
Approx. 2–3 days
Drying Expert Consulting
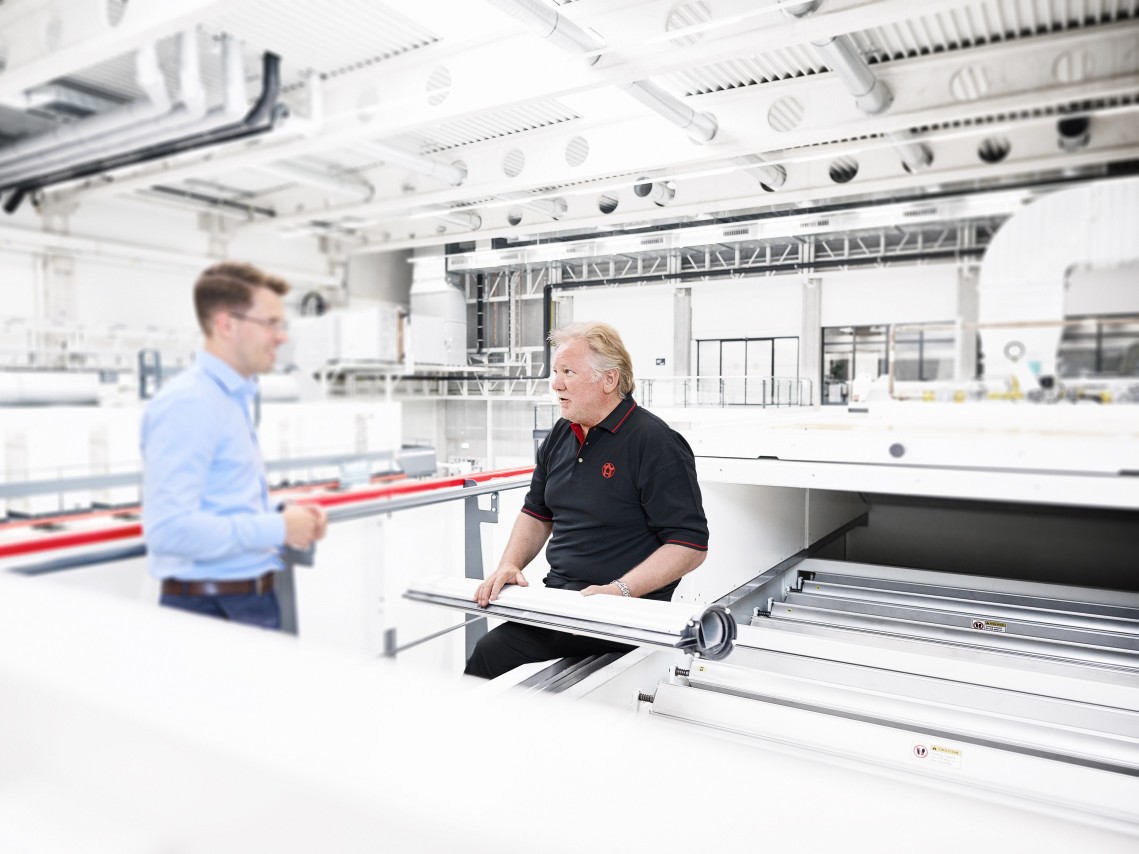
Due to the increasing relevance of energy efficiency and the rapid advancement of technological development, there are many opportunities to improve energy efficiency and performance of your W&H printing machine.To help you identify the individual potential, W&H offers customized consultings by our drying experts.Each generation of printing machines has different savings potentials. These can be matched to individual customer needs such as reducing CO2 emissions, cost savings (e.g. through energy efficiency-related modifications) or increasing the autothermal operating hours of the Regenerative Thermal Oxidizer (RTO).
INSTALLATION
Depending on effort
Ink cooling
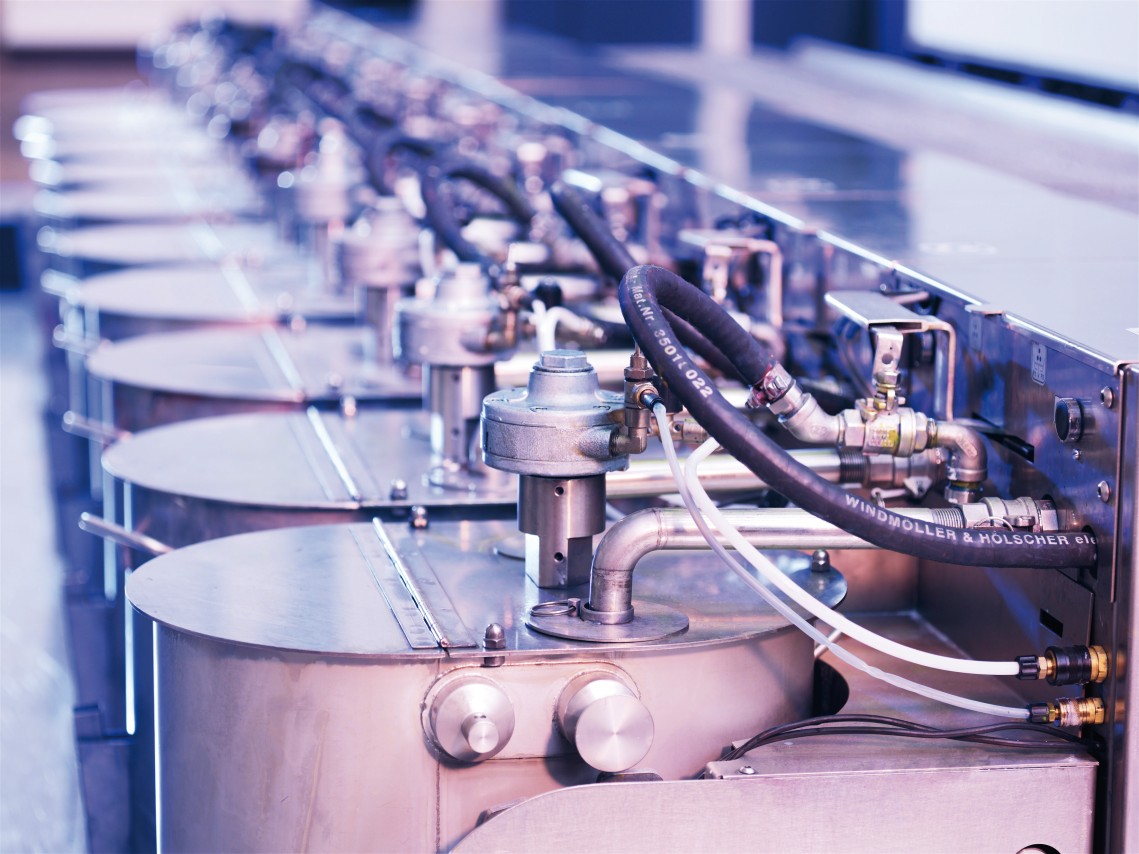
High ink temperatures have a negative effect on the inking process and can cause „ghosting“ effects. In addition, high ink temperatures also increase the solvent evaporation (especially in rotogravure).
INSTALLATION
Approx. 5 days
Independently driven Inking Rollers
Driven inking rollers allow an optimal inking of the cylinders. But different inks require different inking roller speeds for a perfect print result.
INSTALLATION
Approx. 1.5 printing units per day +1 day for integration in PROCONTROL
Repeat length monitoring and control
Repeat Length Monitoring allows continuous measurement of the actual print repeat length during production and displays changes in print repeat length over time (trending). The repeat can also be manually corrected during production without register errors.
Optionally, our Repeat Length Control allows the continuous control of the repeat length and an automatic correction in case of any deviation.
INSTALLATION
Approx. 1 day (remote installation on request)
Insetter controller
The Windmöller & Hölscher insetter controller is used for register-true printing of a pre-printed web during a second web path. The process is predominantly used for printing flexible materials.
INSTALLATION
Approx. 4 days (including training)
Remote calibration of LEL-Sensors
Retrofitting LEL sensors for remote maintenance is much more convenient, saves time and results in significantly less downtime. Our W&H IDC experts are able to read out error and warning messages, perform a soft reset or calibrate the zero and calibration point remotely.
INSTALLATION
Approx. 1–2 days
RGB LAB CHECK
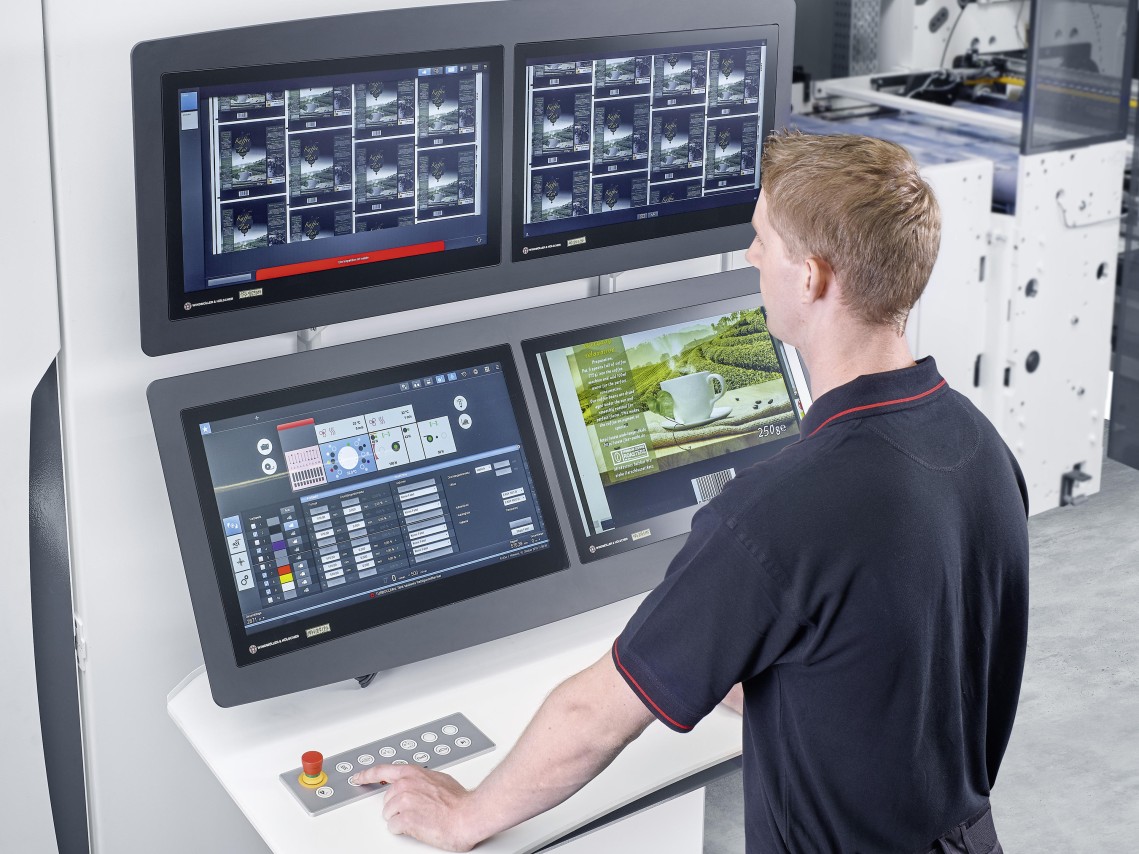
System for relative color measurement and detection of deviations in ΔE, based on RGB sensor data.
Comprising of:
- Trend display ΔE and ΔD
- Visualization in LAB color space
- Limit monitoring with alarm and warning function
INSTALLATION
1 day (remote installation on request)
BARCODE CHECK
- Statistical 1D barcode and 2D/QR code verification using the VISION ZOOM matrix camera
- Real time code quality evaluation in accordance with ISO/IEC 15415 (2D codes) and 15416 (1D barcodes)
- Roll and Job Protocol including barcode statistics
INSTALLATION
1 day (remote installation on request)
PREVENTIVE MAINTENANCE
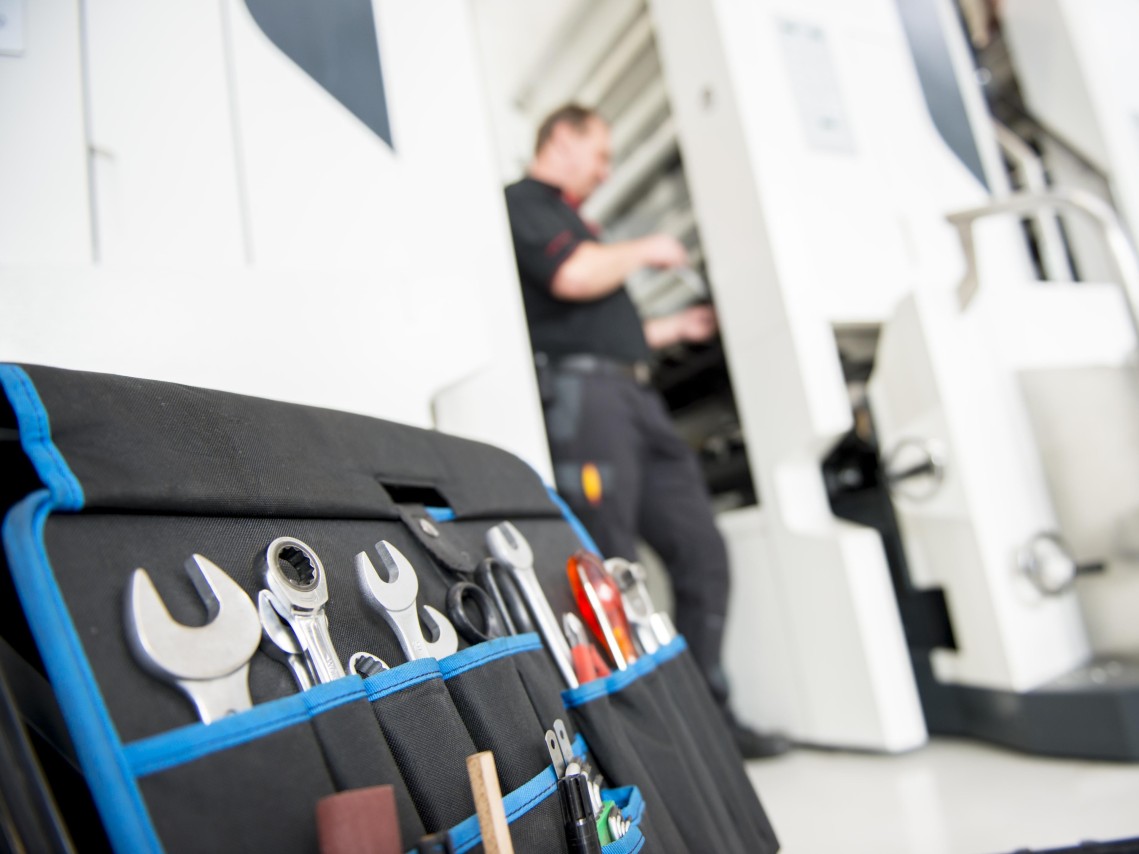
Advisor for upcoming maintenance work, integrated in PROCONTROL.
Detailed descriptions and advices for maintenance procedures, comprising of:
- Safety relevant lubrication
- Standard lubrication
- Inspection of machine components
- Cleaning of parts
INSTALLATION
Approx. 1 day (remote installation on request)
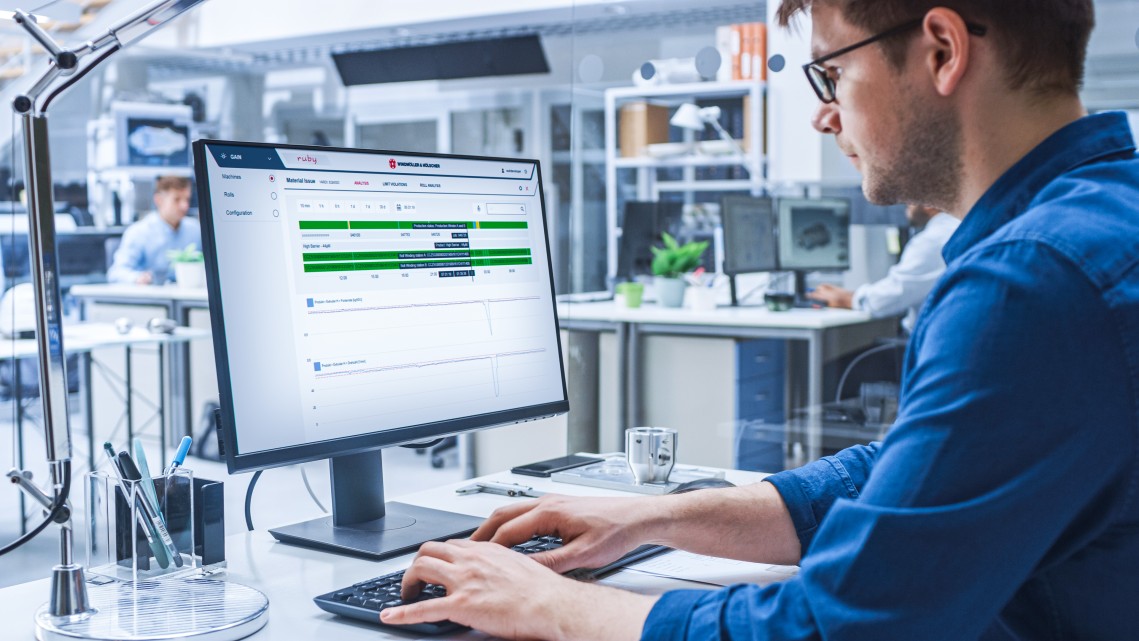
SOFTWARE MODULES
Increase your machine performance with optional software modules by W&H
Benefit from the possibility to increase production quality, machine availability or efficiency of your extrusion line or printing press even more easily. Direct online access to your machine allows you to add new features or connect to RUBY, the W&H IoT system, without requiring hardware or an on-site visit.
Using a secure internet connection, W&H specialists can connect directly to your machine and modify the software configuration. This enables the installation and commissioning of new features, e.g. RUBY, BARCODE CHECK, RGB-LAB CHECK and many more. After successful commissioning, W&H provides your machine operators with helpful information to efficiently use the newly installed functions.