Lifecycle Services lead to less downtimes
Individual service visits increase the performance of both W&H blown film lines and W&H flexo press at Jayshri Propack.

Jayshri Propack, located in India, is a flexible packaging film manufacturing company. It is specialized in multilayer barrier and high performance films for various applications in the food supply chain, FMCG packaging and other industries. As Jayshri Propack has the capability to extrude, laminate, convert and print all the films it produces, it has a well-equipped W&H machine park consisting of a VAREX´´ blown film line, two AQUAREX watercooled blown film lines and a MIRAFLEX´´ flexographic printing press. To maintain high output on either the extrusion lines or the flexo printing press, unplanned downtime must be minimized. With this in mind, Jayshri contacted the W&H team in India. In joint discussions, the requirements were further defined and measures derived. The result was a service agreement within the framework of W&H Lifecycle Services.
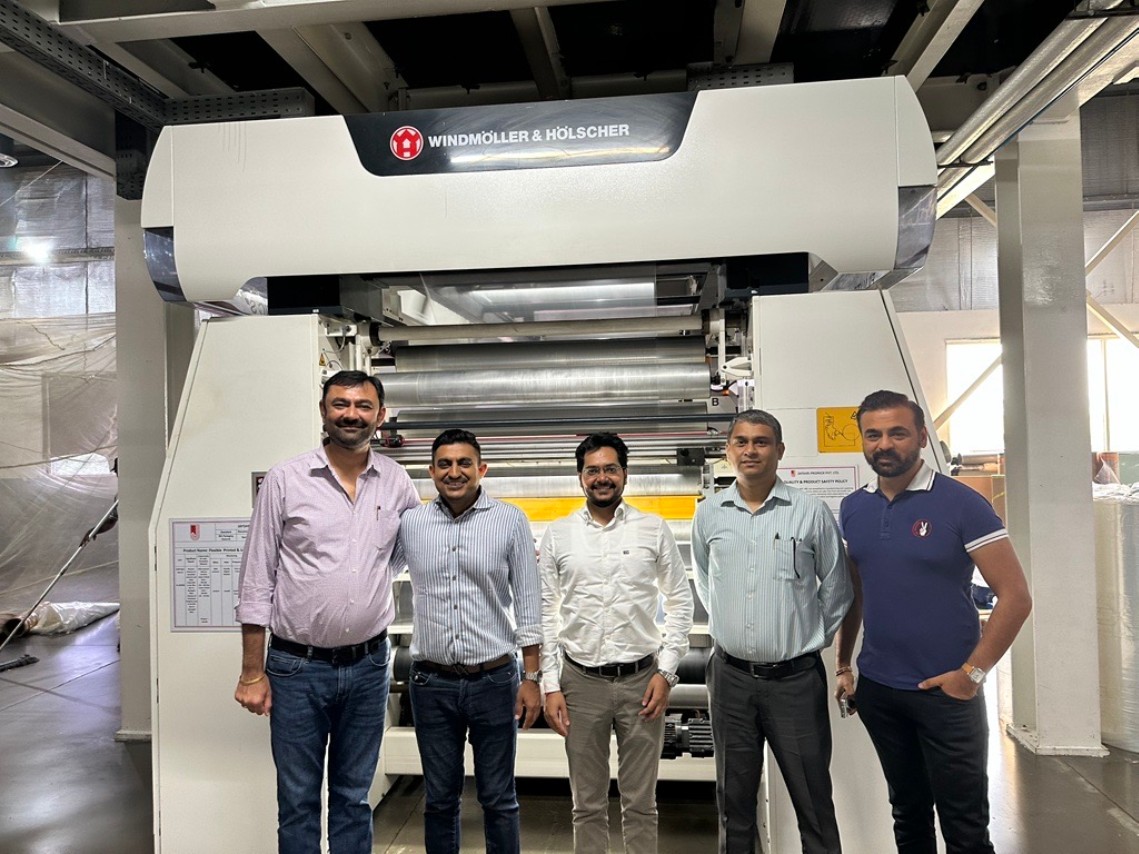
W&H Lifecycle Services
With Lifecycle Services, Windmöller & Hölscher has launched a service concept that can be individually adapted to the customer‘s needs and that focuses on the high performance of W&H machines throughout their entire lifecycle. Regular, proactive visits by our service technicians enable us to identify problems with the machines at an early stage and take appropriate countermeasures.
Individual design of Lifecycle Services
Jayshri Propack opted for a Lifecycle Service with three visits per year by W&H service technicians. The service visits for the blown film lines and for the flexo printing press are scheduled separately as required. The customer prepares the visits by collecting the open points to be addressed. Much is possible, from the check of neuralgic machine components and minor repairs to the joint optimization of machine settings. Maintenance support also includes recommendations for necessary spare and wear parts. The open points list is continuously updated and processed. All these measures have led to a continuous improvement in machine condition, performance and availability. This has also demonstrably reduced repair and maintenance costs.
Jignesh Hirpara, Director at Jayshri Propack is convinced of the W&H Service: "W&H Lifecycle Services has brought immense benefit and helped us reducing unplanned downtimes."
Recommendations for die cleaning service
During the W&H service technician‘s visits, further recommendations are made to identify actions that can be taken to maintain or improve performance. In the case of Jayshri Propack, for example, attention is paid to the quality of the blown film produced. If the profile starts to look bad, or if particles appear on the die, this is a sign to have the die head professionally cleaned. In this case, a separate appointment is made for die head cleaning service at Jayshri. The W&H experts help on site to clean and maintain the heart of the extrusion line in a professional manner that is gentle on the material.
The regular Lifecycle Service visits have established a close relationship of trust between Jayshri Propack and Windmöller & Hölscher. Both companies look forward to continuing their cooperation with the aim of continuously optimizing production.