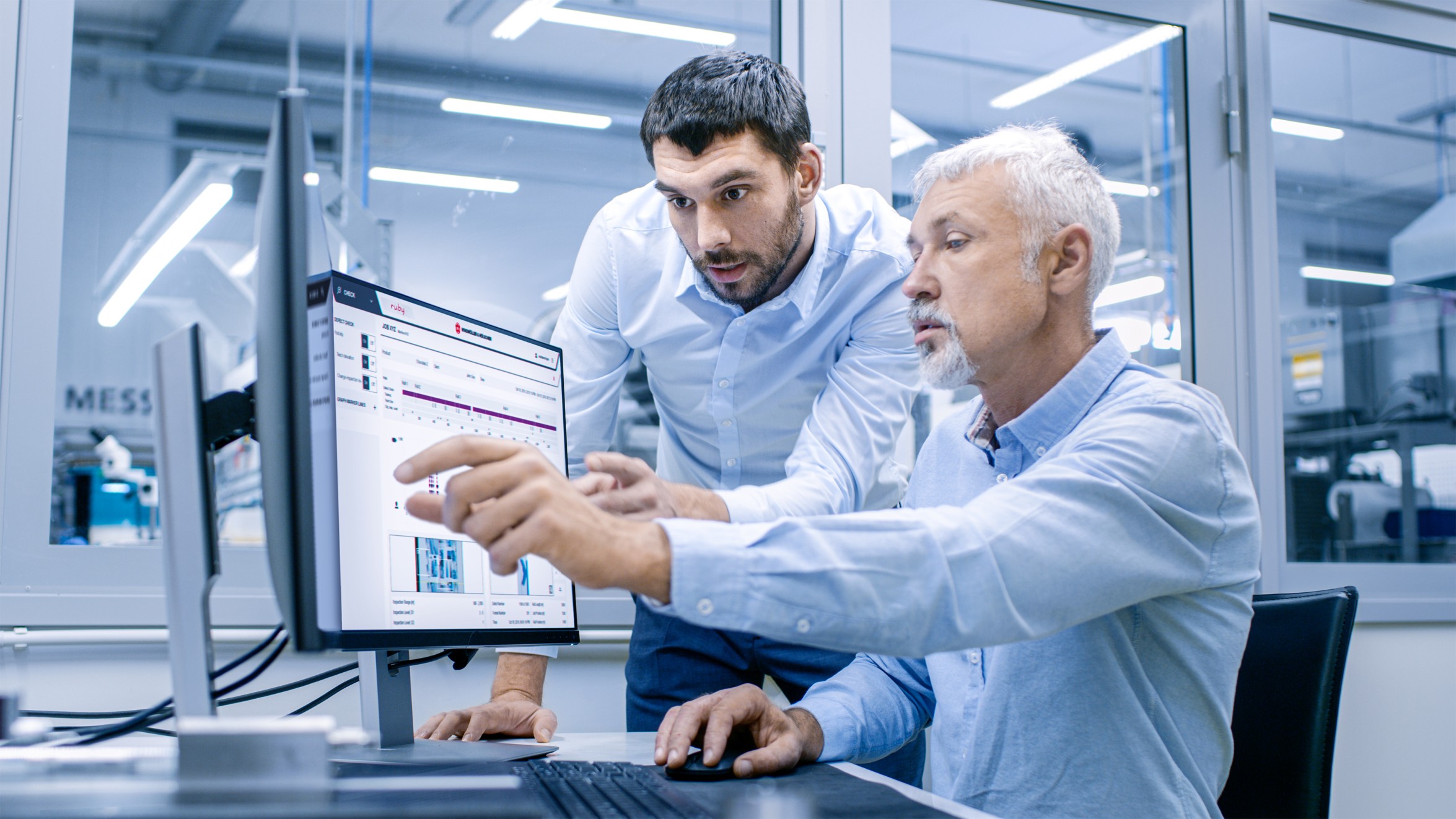
At a glance
Product information
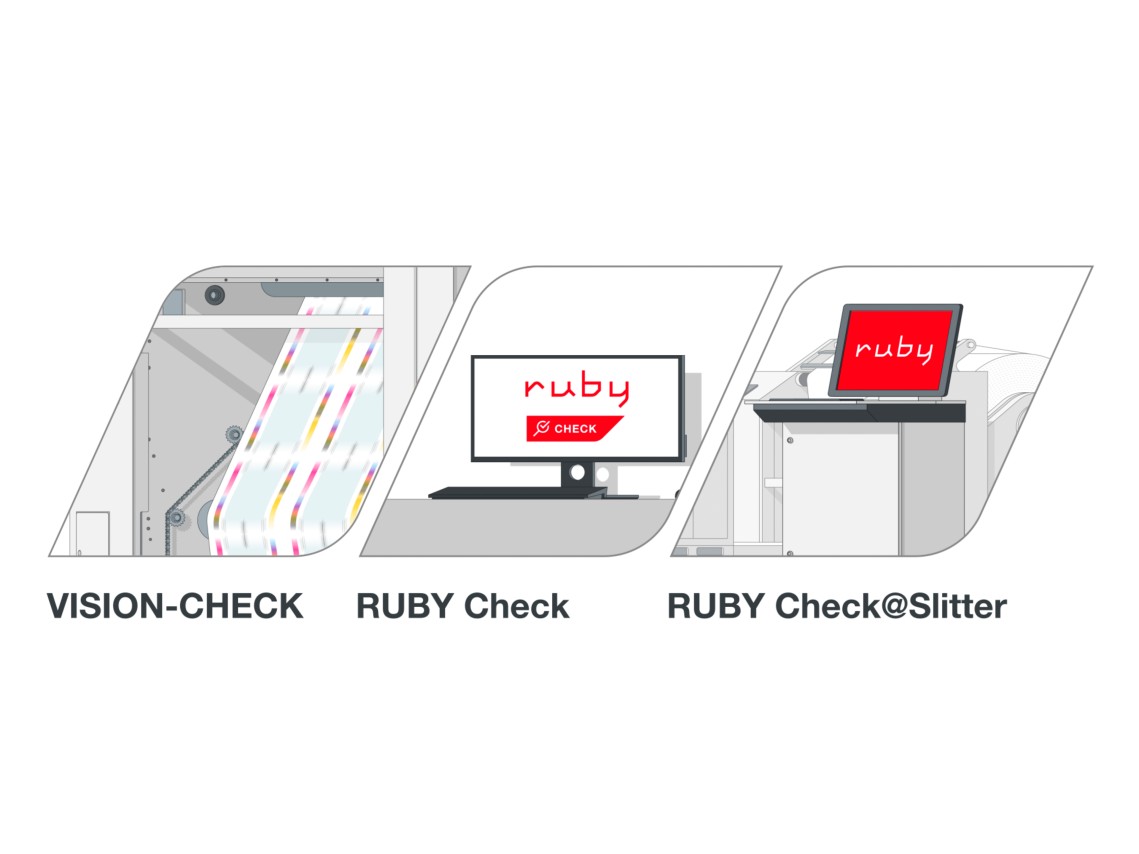
RUBY Check – improve your package printing
Deepen the functionality of W&H’s inspection system VISION CHECK with RUBY Check and store your print inspection data central for at least one year. Assess completed jobs conveniently from your office and leave quality control to quality managers. Decide subsequently which printing defects are significant. An intuitive interface enables an efficient and time-saving way of working. See all possible defects at a glance with our new defect heatmap. RUBY Check knows your machine data: Compare the trending of all machine parameters and print defects and identify incorrect machine settings or operating procedures as a root for print defects. Optimize your processes and become more efficient. Speed up your Downstream Processing with RUBY Check@Slitter and optimize your end-to-end workflow to reuse defect detection data from the printing machine.
USE CASES WITH RUBY CHECK
1. Traceability and Claim Management
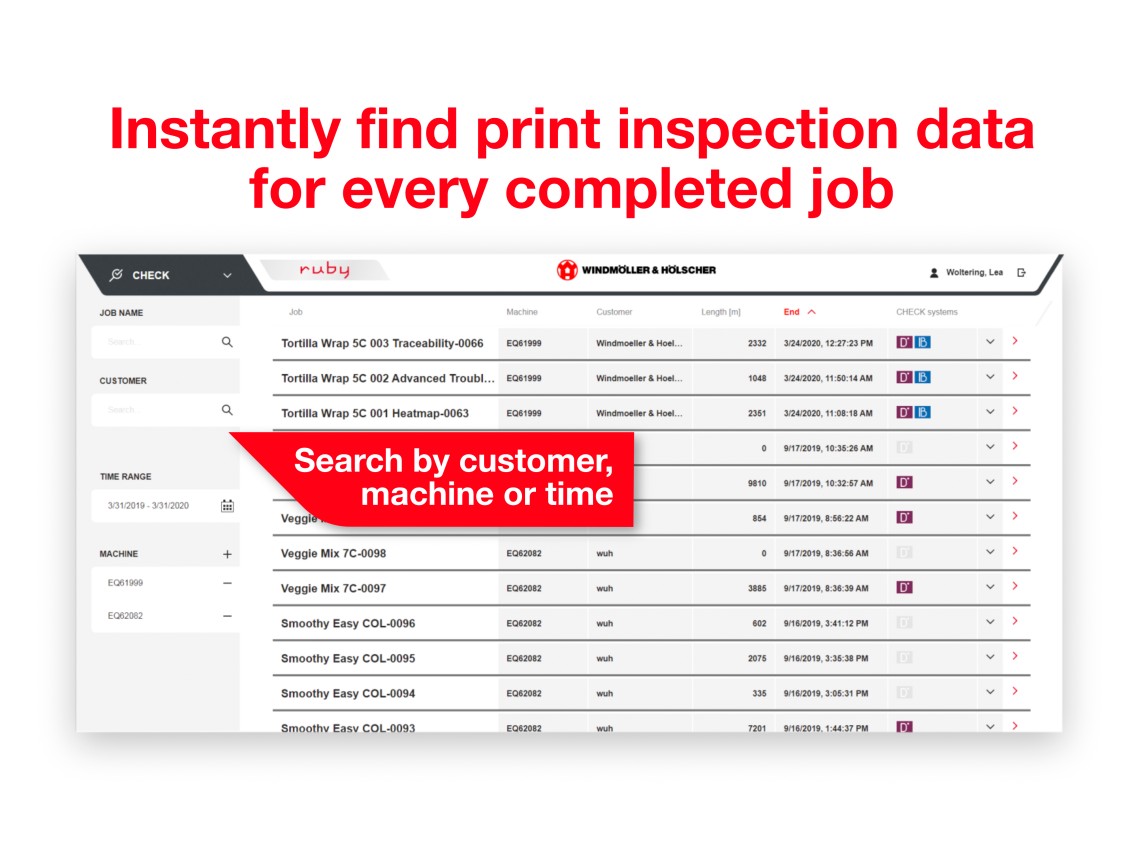
- Guarantees complete traceability of the inspection data for at least 1 year.
- Detailed roll- and job reports.
2. Remote Quality Assessment
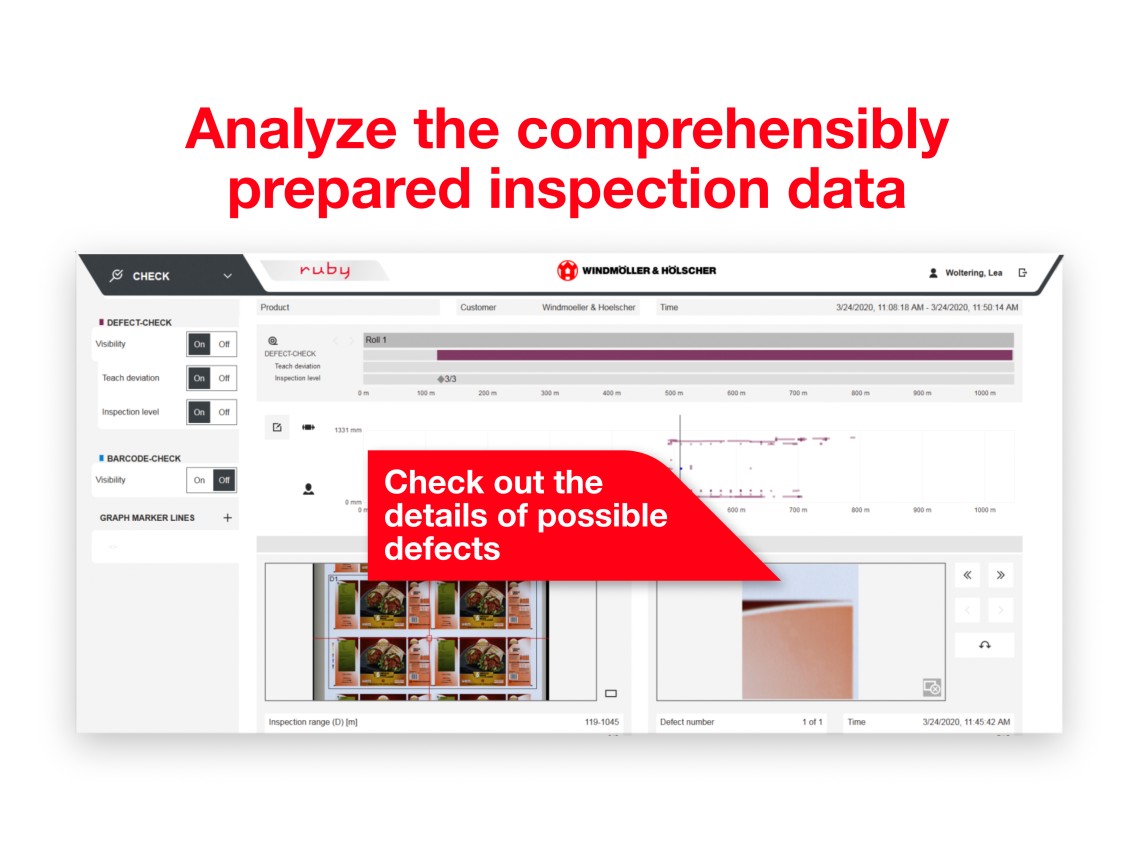
- Leave quality control to quality managers
- Review, analyse and process your print inspection data remotely for increased production efficiency and print quality
- Find all possible defects at a glance with our new defect heatmap for highly efficient assessment of your inspection data
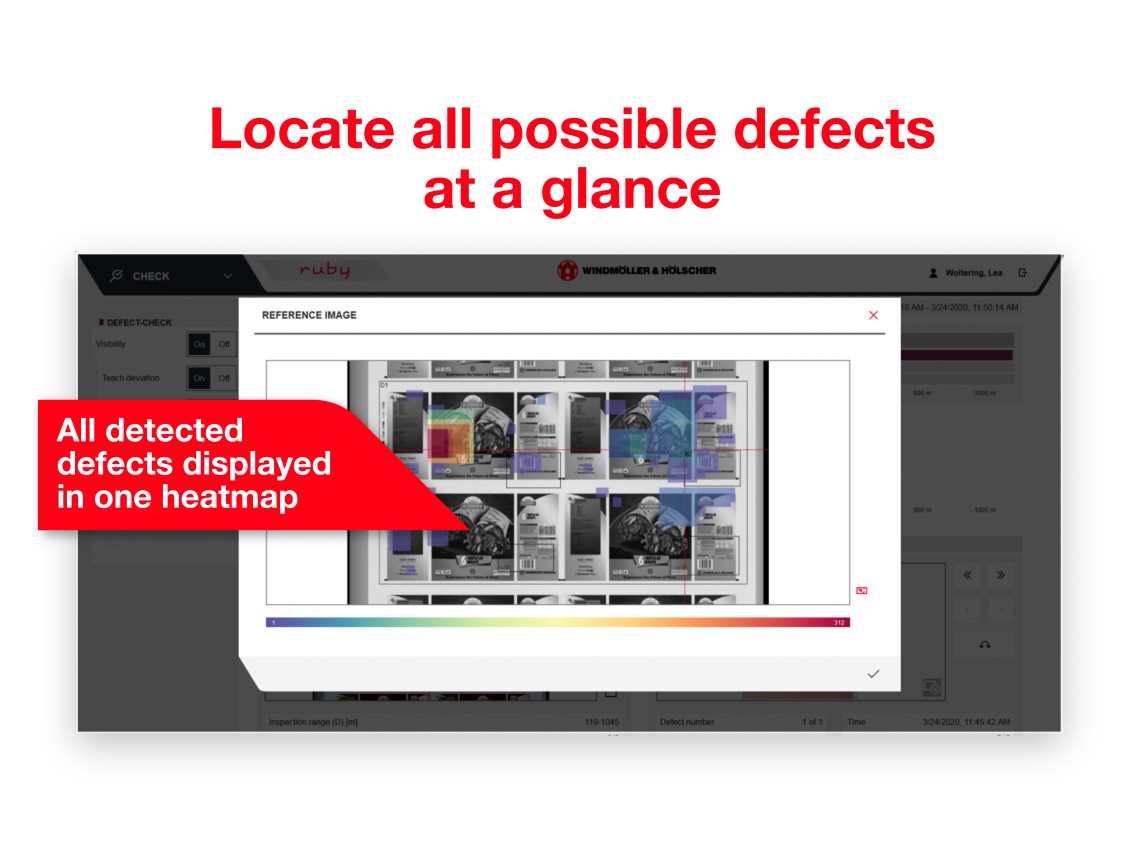
3. Root Cause Analysis
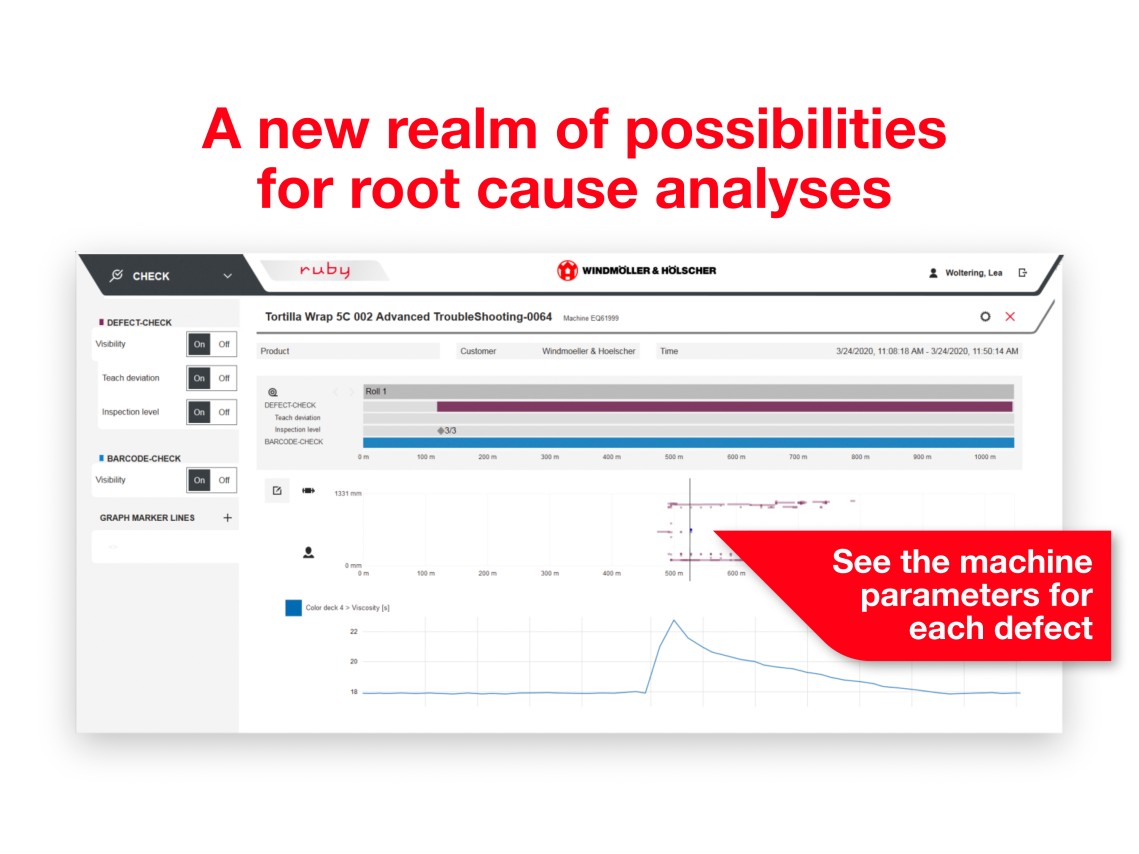
- RUBY Check is fully integrated into the W&H world
- Overlay machine parameter trending and print inspection data for root cause analysis
- Optimize your processes and become more efficient
4. Downstream Processing with RUBY Check
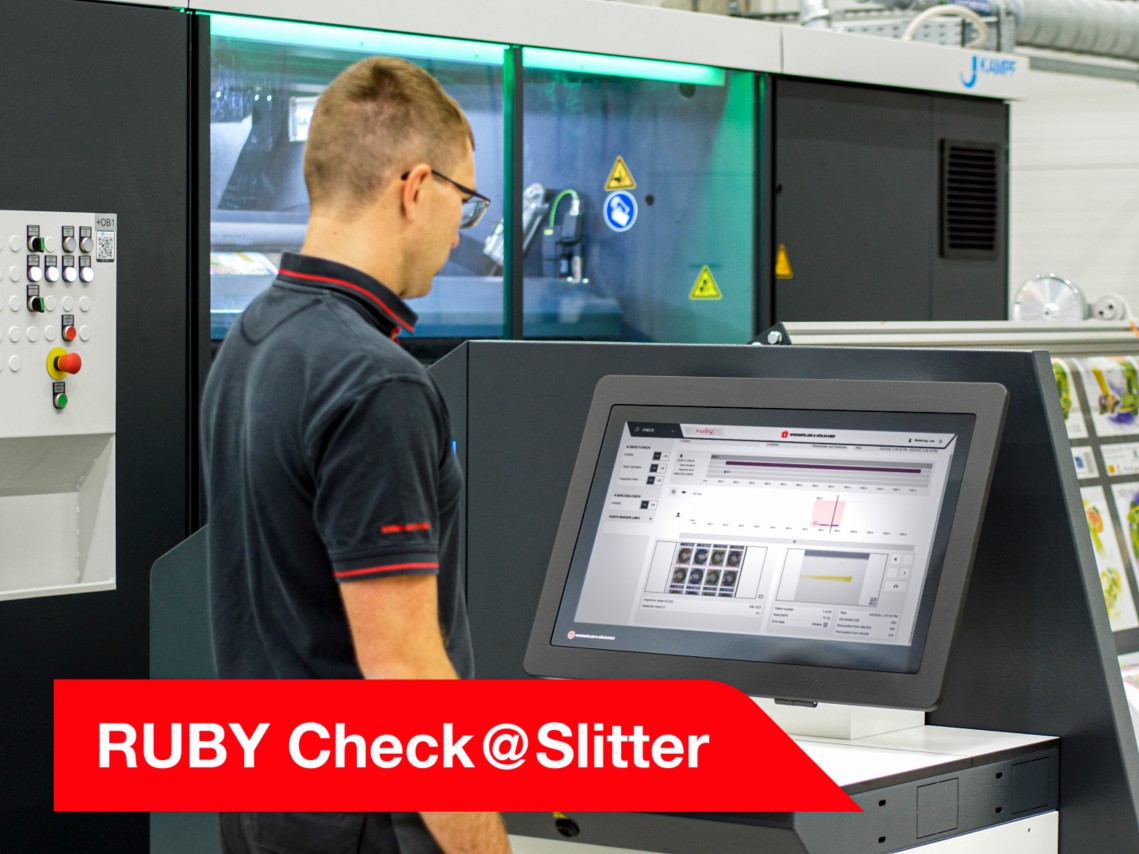
Speed up your Downstream Processing with RUBY Check
Optimize your end-to-end workflow to reuse defect detection data from the printing machine. Use the W&H’s new Inkjet Marking System integrated in your printing press to mark your jobs for safe position tracking of defects by means of meter markings, completely independent of a starting position.
W&H’s print inspection system VISION CHECK detects print defects, which you can assess conveniently from your office with RUBY Check. Define waste areas which should be removed.
With RUBY Check@Slitter you can locate this print defects easily in further process steps (slitter, rewinder…) fully automatically. The Mark Reader positioned in your processing machine identifies the job and the job position based on the inkjet marking. The processed data is automatically called up and displayed at the RUBY Check Terminal on the processing machine. RUBY Check controls the processing machine and stops at the correct position automatically to the desired position (if supported by manufacturer) for efficient and time-saving processing.