RETROFIT SOLUTIONS
New Modules for Your Blown Film Lines
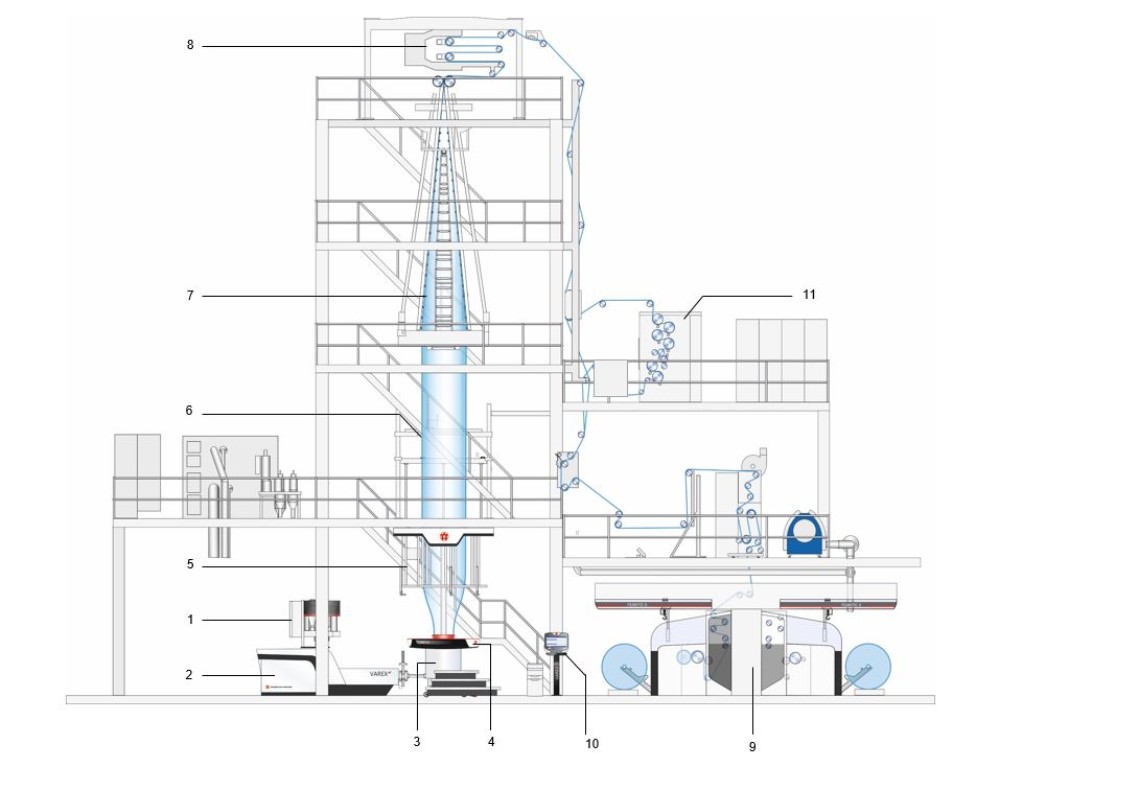
1. Gravimetric resin metering and throughput control, 2. Plastifying units (extruders, screws, etc.), 3. MAXICONE die heads, 4. ARCTIS air rings to increase output in conjunction with patented gauge profil controllers, 5. VARIOCAGE film sizing unit, 6. Thickness gauges (contact, non-contact, traversing), 7. Haul-off units and appropriate components, 8. reversing haul-off unit, 9. Winder add-ons, 10. PROCONTROL TS operator console and OPTIFIL PLUS process automation, 11. MDO
Easy2Change
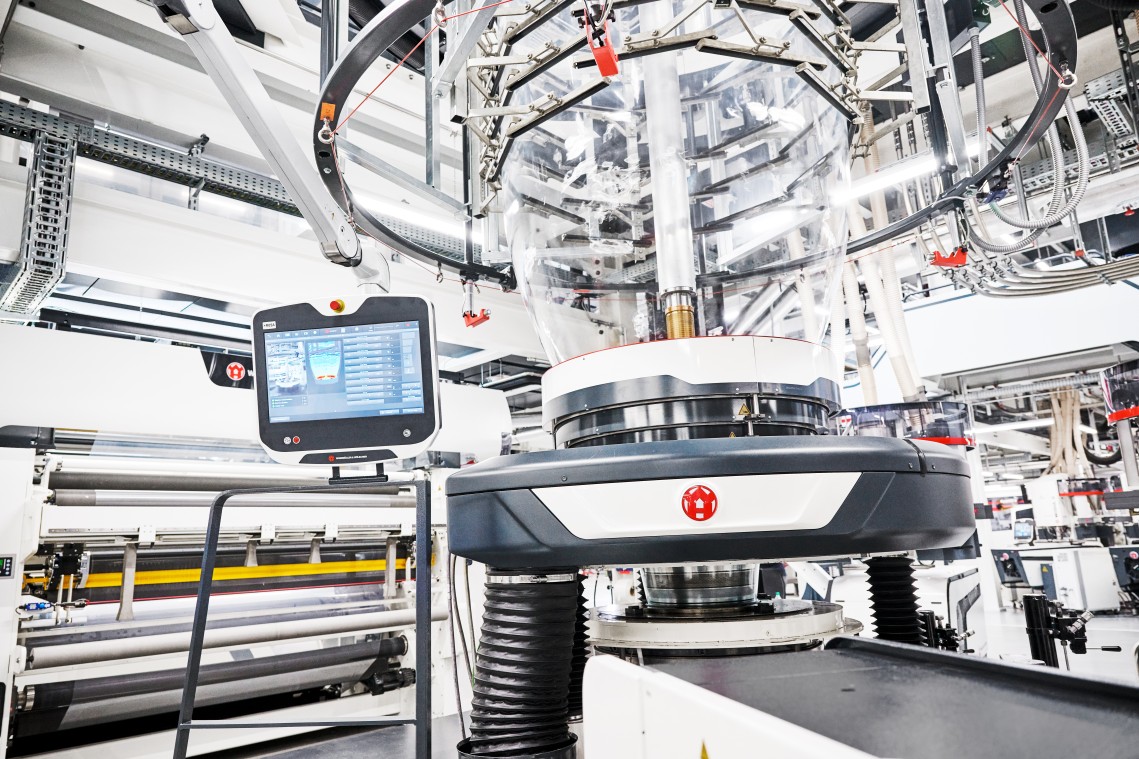
Easy2Change as a Retrofit
EASY2 Change accumulates all existing W&H automation modules that ease the changeover process (like PROFILE BOOSTER, EASY CHANGE, …), adds a two camera-based optical sensing system and a fully motorized, encoder controlled and recipe integrated ARCTIS II air ring plus the new PROCONTROL dashboard.
It reduces your waste generated during every changeover phase and eliminates errors by guiding your operator through the process using the intuitive dashboard. No room left for unforced errors resulting in every changeover to be spot-on the first time, every time.
The retrofit package contains two cameras (optical and thermal), the ARCTIS II motorized air ring and the PROCONTROL dashboard software.
Recently delivered VAREX II and OPTIMEX II machines can be retrofitted easily. For machines delivered before 2021, please ask your W&H contact for further details.
New Gravimetric Weighing System and Vacuum Feeders
New gravimetric system (module G) and vacuum feeders can be retrofitted to all W&H blown film lines as well as extrusion equipment of other manufacturers.
Installation
Installation of gravimetric system and vacuum feeders, including all components, will be done by W&H service technicians.
Installation: approx. 1 – 2 days per gravimetric system and vacuum feeder (including training)
VAREX Extruders
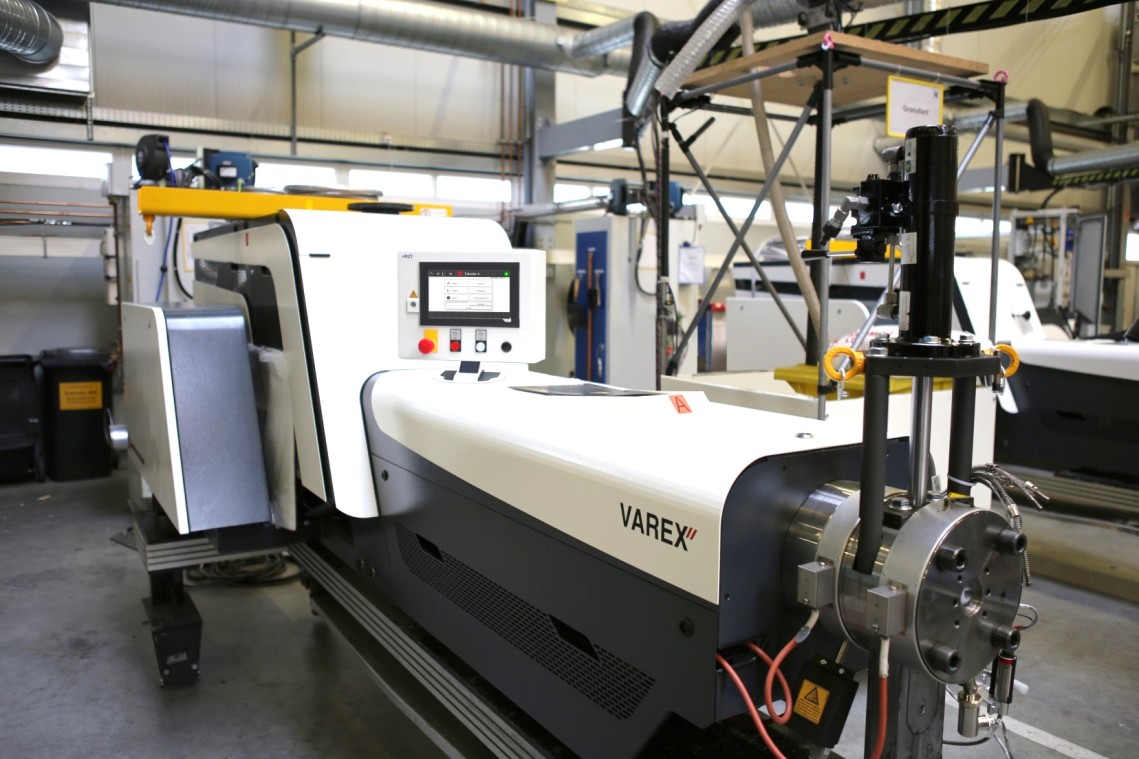
VAREX retrofit extruders are available for all W&H lines and for extrusion equipments of other manufacturers.
Installation
Installation of extruders, including all components, will be done by W&H service technicians.
Installation: 1 – 2 days per extruder (including training)
New MAXICONE Die Heads
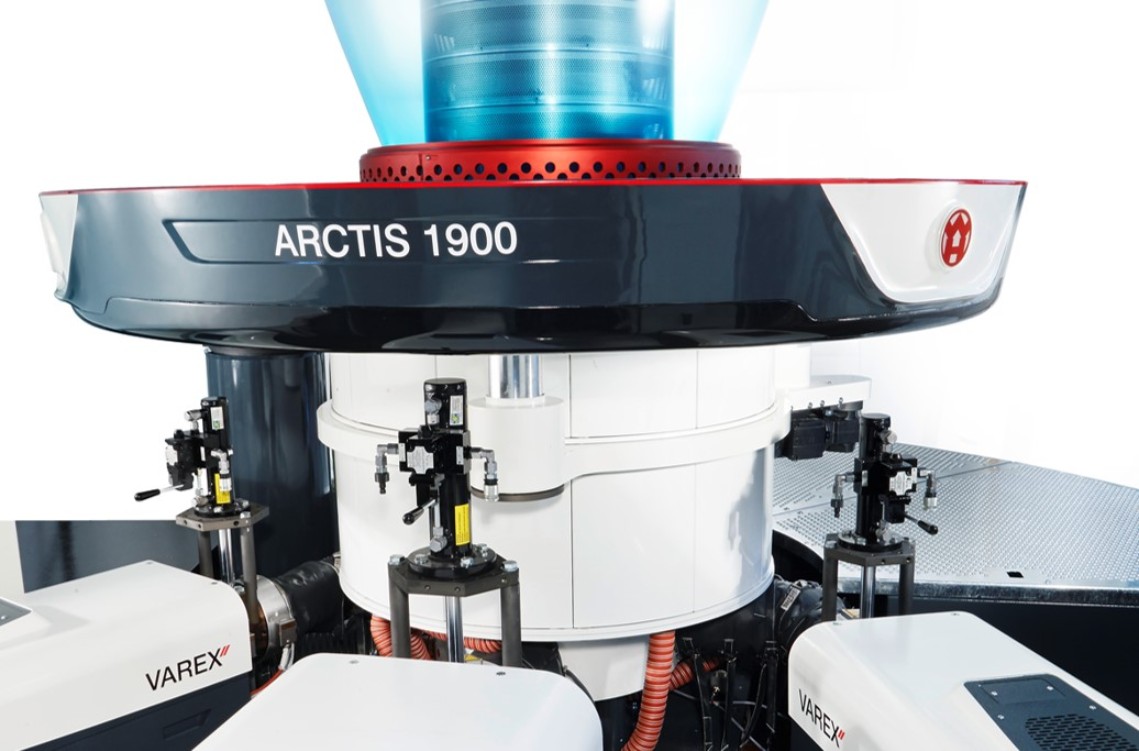
Outstanding film quality and minimal changeover times are the result of MAXICONE die heads. All W&H blown film lines as well as other manufacturers extrusion lines can be retrofitted with these die heads.
Installation
Die head installation, including all necessary components, will be done by W&H service technicians.
Installation: approx. 5 days (including training)
ARCTIS Air Ring
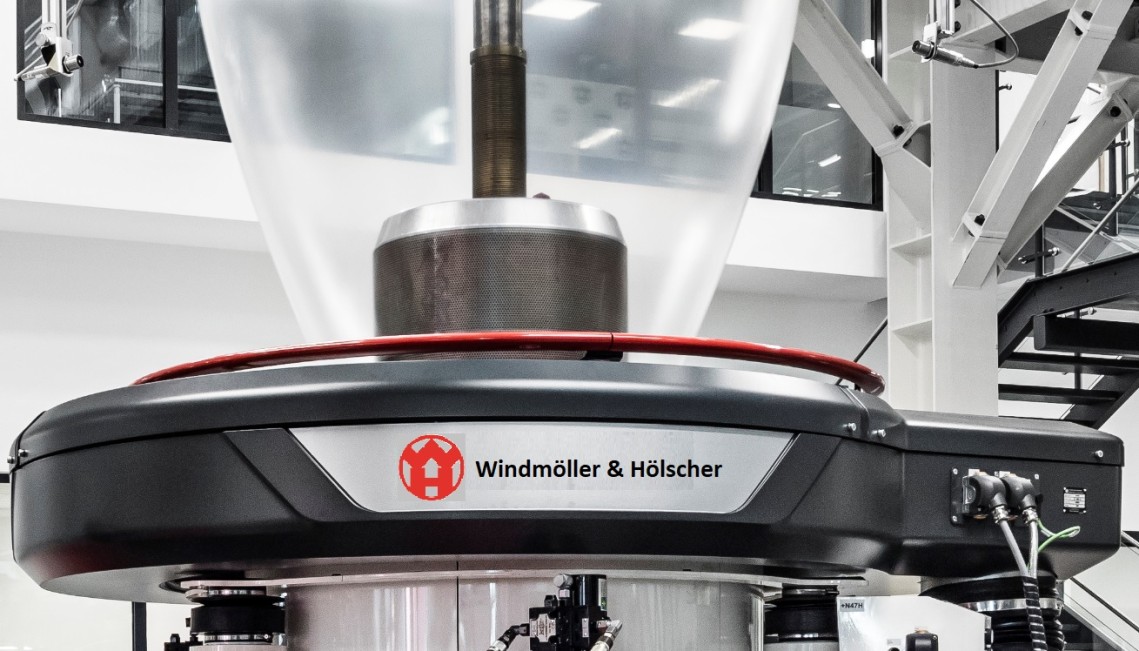
Boost your output and improve your film quality by retrofitting W&H dies or ARCTIS air rings. A new gauge profile controller is available as an additional option.
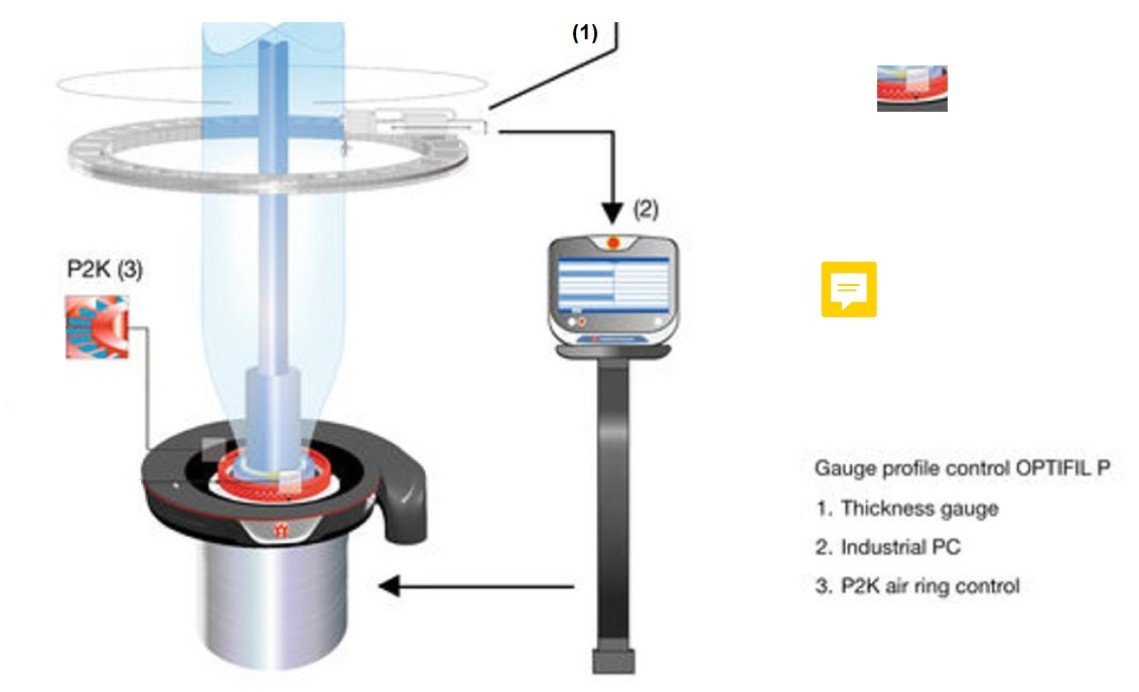
Installation
Installation of ARCTIS retrofit packages, including all components, will be done by W&H service technicians.
Installation: approx. 5 days (including training)
VARIOCAGE
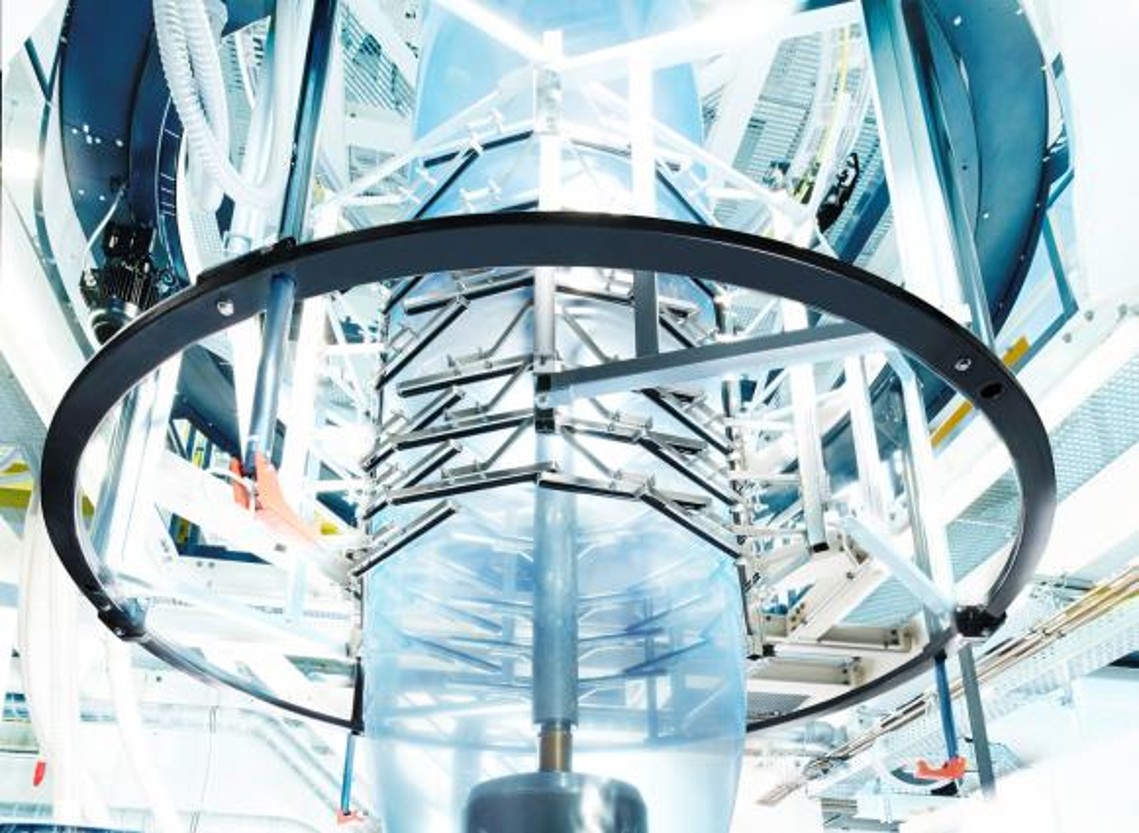
Improve film width tolerances with optimal calibration that saves trim and satisfies your customers with its operating properties.
Installation
The film calibration unit and components are assembled by W&H service technicians.
Installation: approx. 2 days (incl. training)
PROFILE BOOSTER
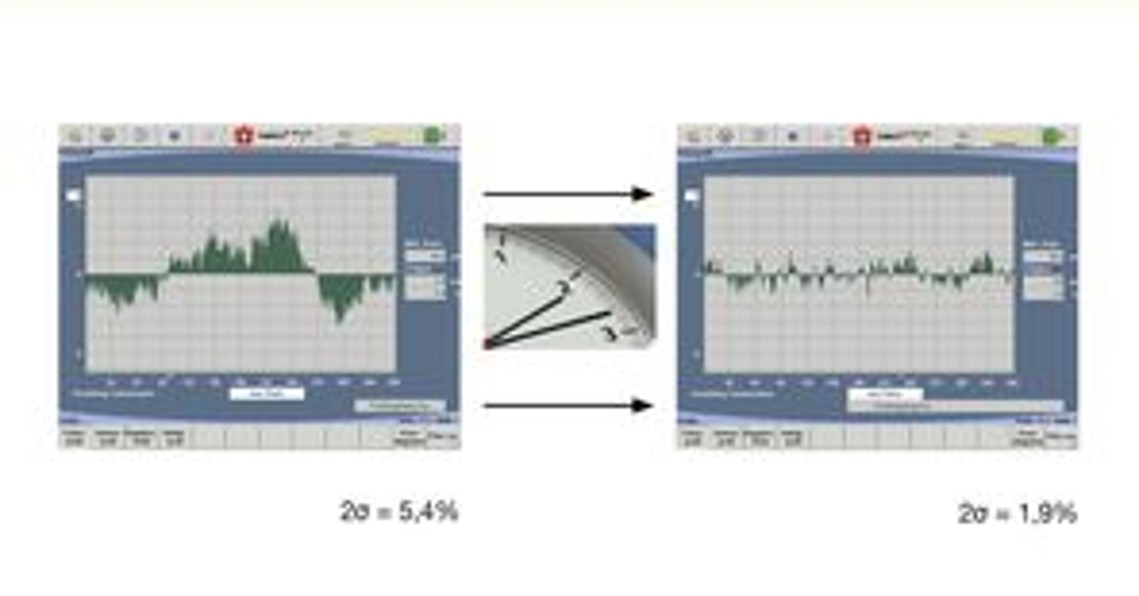
Increases the effective up-time of your blown film line through intelligent die and/or air ring control at line start, ensuring fast saleable quality production and short job change times.
Installation
Adaptation of existing control system and change of hardware components (if necessary) will be done by W&H service technicians.
Installation: approx. 1.5 days (including training)
MMC Retrofit
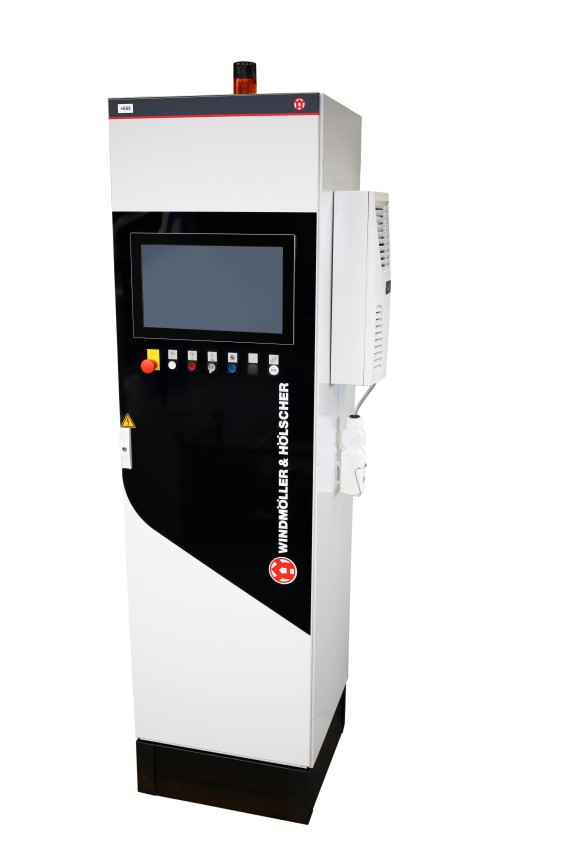
Get ready for the future and improve your production by replacing the MMC control technology, which has been discontinued for years, with the latest PROCONTROL TS automation.
Installation
Retrofitting of control hardware and of appropriate operator control elements will be done by W&H service technicians.
RMOS-IPC Retrofit
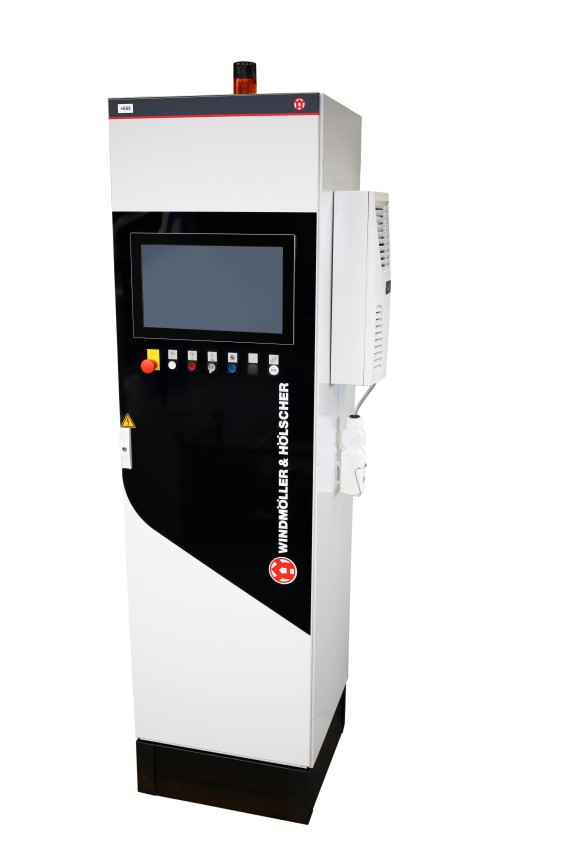
RMOS-IPC Retrofit
Get ready for the future and improve your production by replacing the RMOS-IPC control technology, which has been discontinued for years, with the latest PROTCONTROL TS automation.
Installation
Retrofitting of controlhardware and of appropriate control elements will be done by W&H service technicians.
Installation: approx. 1 day (including training)
RUBY Retrofit
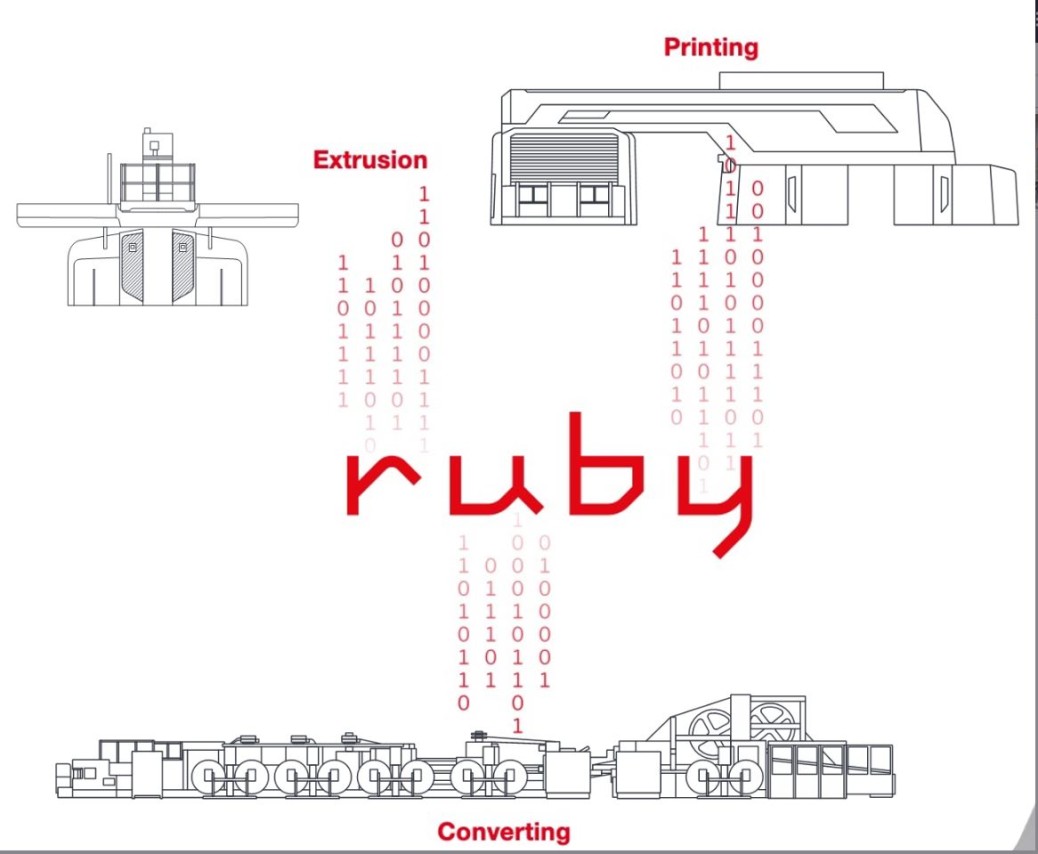
The new IoT-system RUBY allows monitoring, automating and improving your packaging production - or as we call it:
Dig Data. Do Better.
RUBY Retrofit
Installation: approx. 1 day (including training)
Module XTENSION
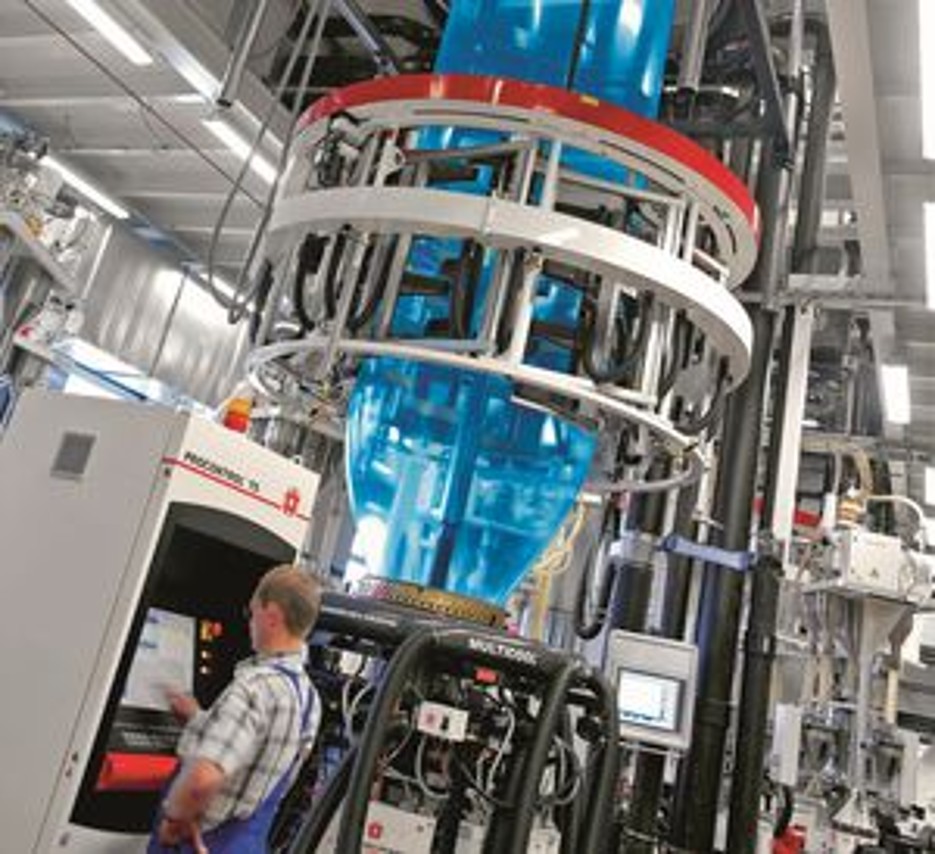
This module allows for easy integration of customer supplied components such as vacuum feeders, gravimetric systems, chillers, draws, winders, etc. into VAREX blown film extrusion lines.
Installation
For electric interfacing of customer supplied components with the PROCONTROL TS column, B&R control modules will be provided and installed. Installation of the necessary software will be done by W&H service technicians.
Installation: approx. 1 day (including training)
Machine Direction Orientation (MDO)
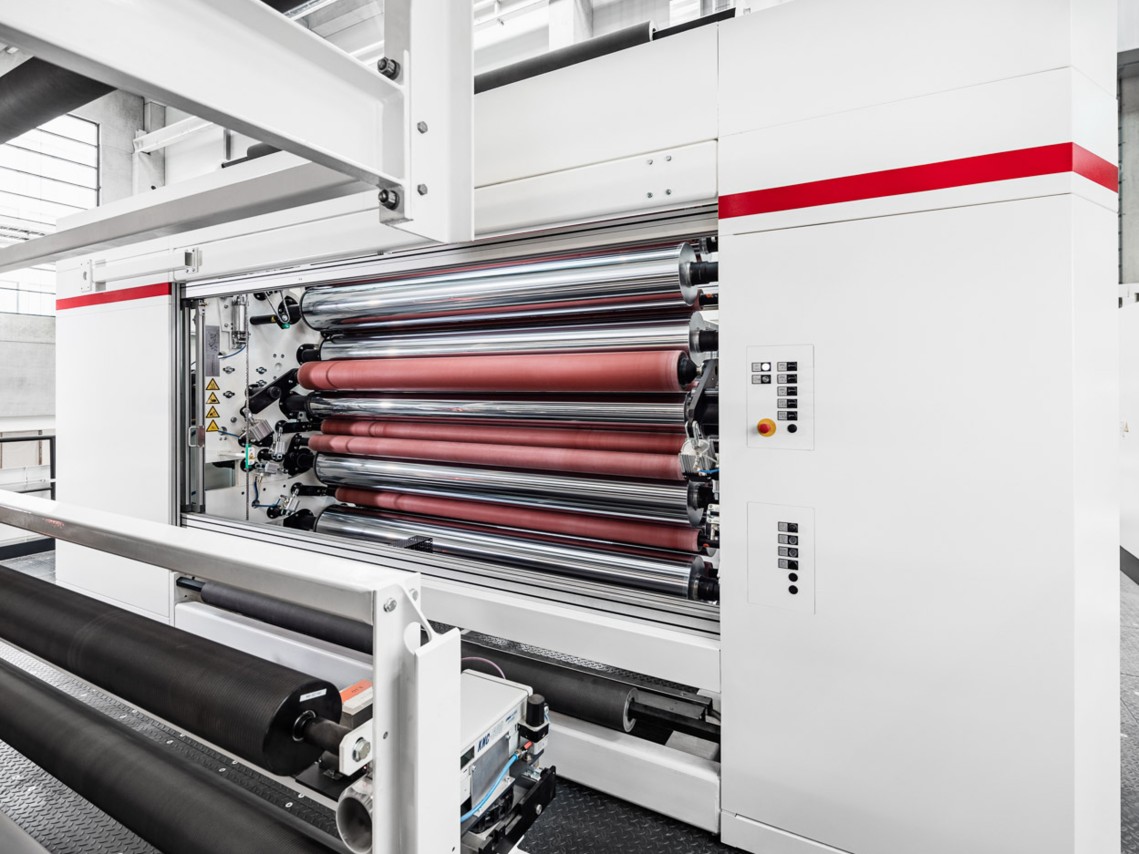
MDO (Machine Direction Orientation) from W&H can be retrofitted to both cast and blown film lines. The process improves barrier properties and gives mono- and coextruded films improved strength and stiffness, better shrink properties and more gloss and transparency.
Installation
Installation of MDO will be done by W&H service technicians.
Installation aaprox. 8 days (including training)
TURBOSTART
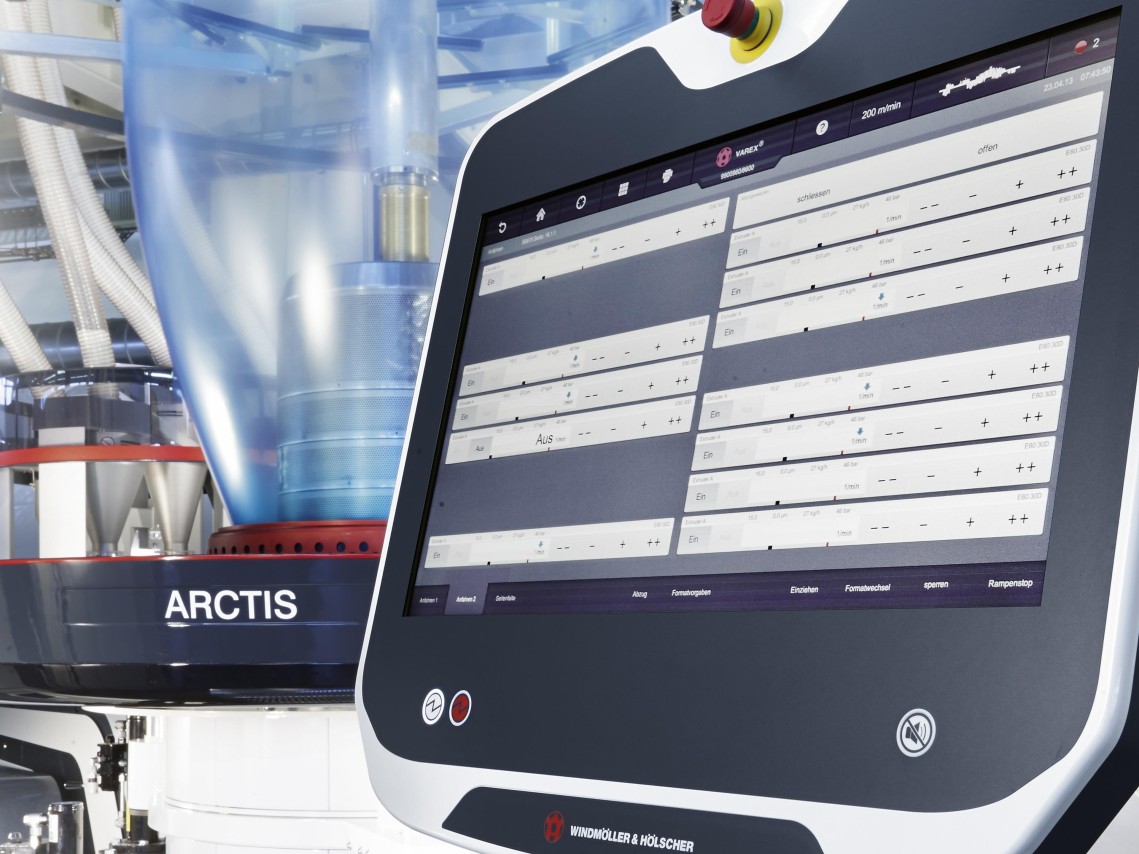
TURBOSTART
The automation module that automatically stops and starts your VAREX II line with the touch of a button
The new automation modules TURBOSTOP and TURBOSTART support the operator in shutting down and starting up the line in a simple seven-step approach. The intelligent interaction between software and dedicated hardware components ensure an automatic process from shutting down all machine components, securing the film in the line and starting up all components again, until the line is running again.
- Fastest possible shutdown and start-up process for a more efficient production
- Minimal operator involvement for ensuring process stability and high end product quality
- Enhanced operator safety through less knife usage during start-up process Compared to a manual shutdown and start-up, more than 50 % time is saved.
FILMATIC-Winders
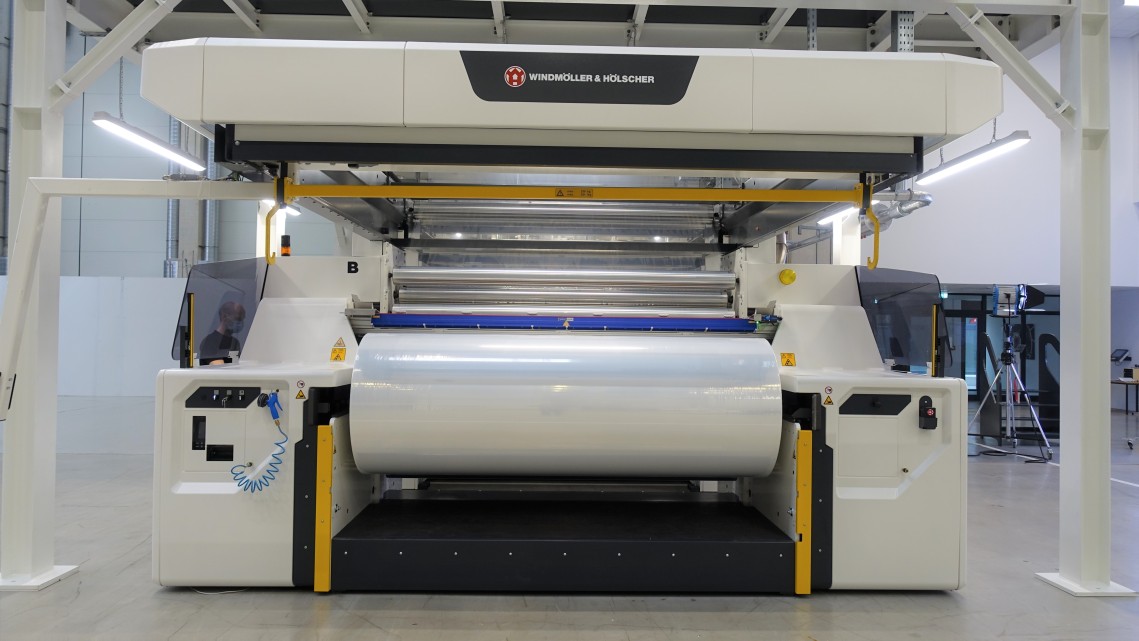
Easy processing with a smart design: With a film winder from W&H's comprehensive FILMATIC range, you can offer perfect, straight-edged rolls from start to finish.
Retrofittable to every blown film line.
Installation
Filmatic winders and components are assembled and installed by W&H service technicians
Installation including training: approx. 5 days (depending on requirements)
FILMEX Extruders
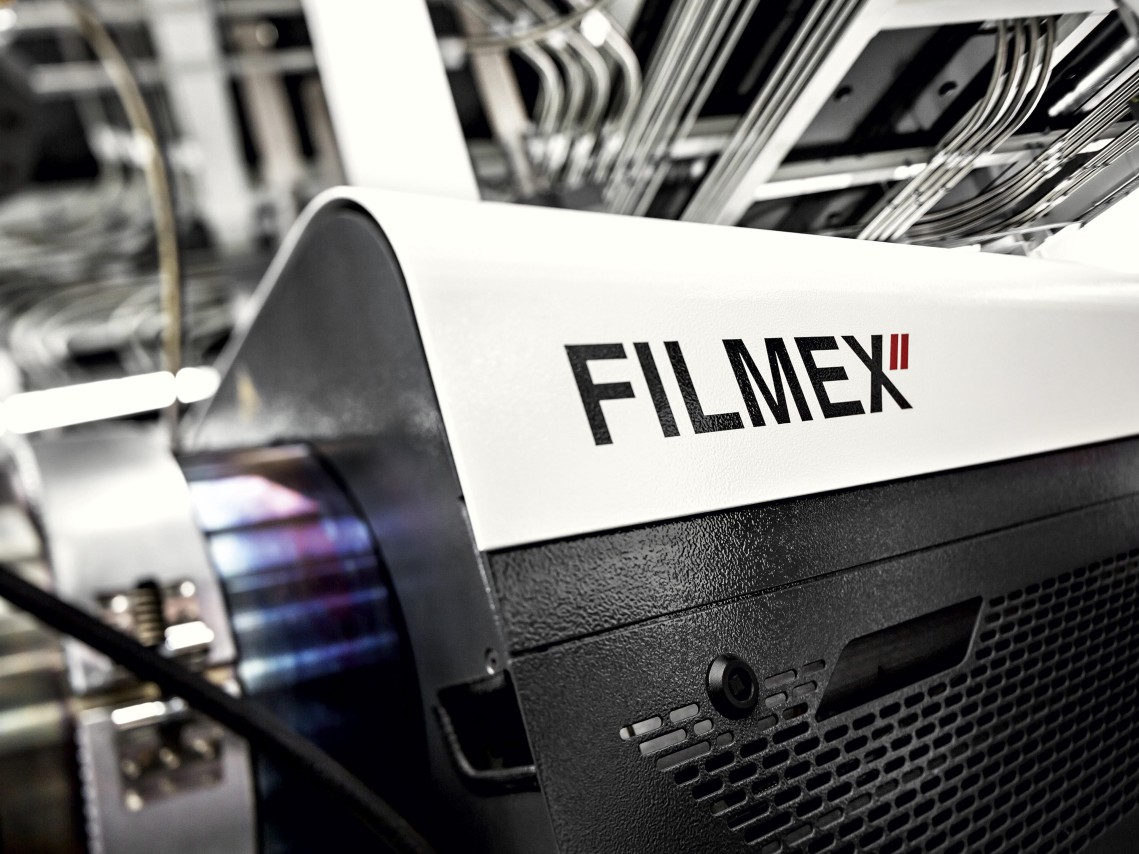
Upgrade your cast film line by retrofitting high performance FILMEX extruders with SMB (Smooth Barrier) screws and crosshole mixing sections.
Installation
Installation of extruders including all components either by W&H service technicians or by customer.
Installation: approx. 1- 2 days per extruder (including training)