RETROFIT SOLUTIONS FOR W&H CONVERTING MACHINES
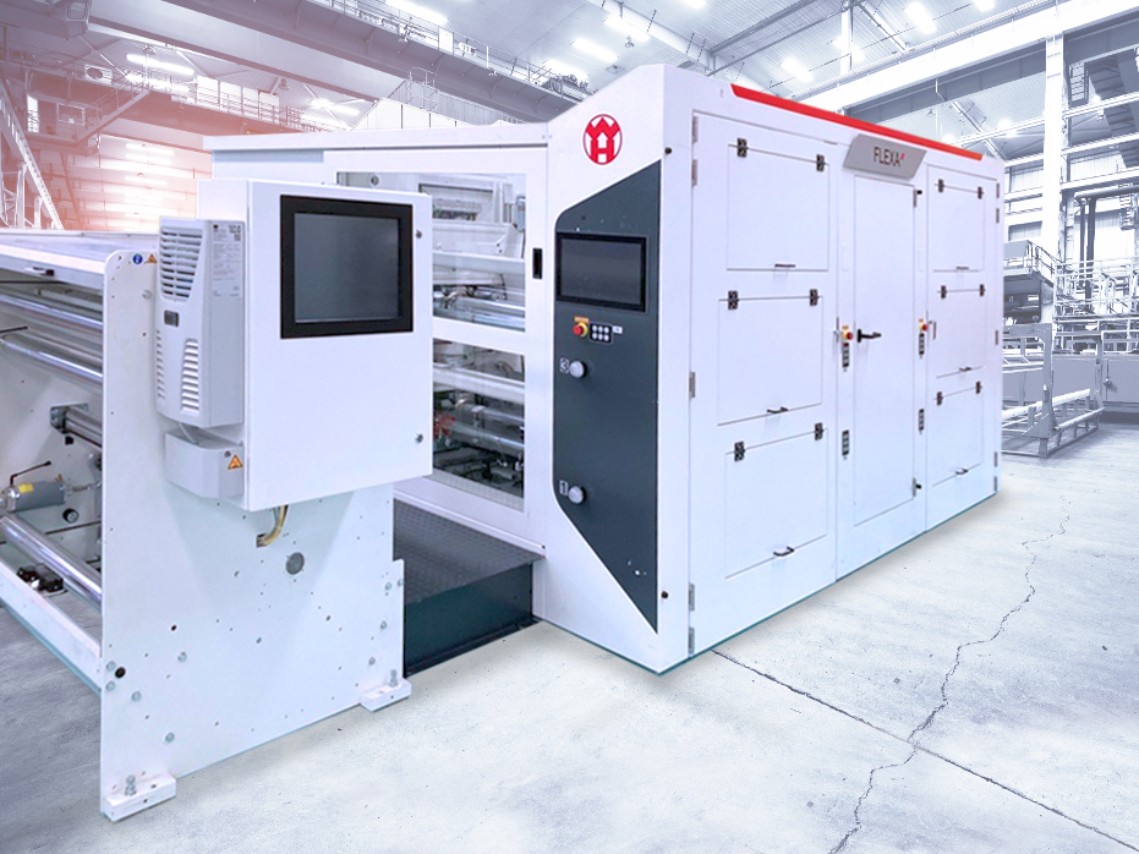
High efficiency, top quality and maximum flexibility at low prices - the market demands highest performance from flexible packaging manufacturers. However, investing in new machinery is not always the best solution to meet these requirements. With our retrofit solutions, new functions or modules can be added to existing converting machines. The development of customer-specific special solutions is also one of our core competencies. This enables you to react to new challenges at any time.
Our retrofit solutions address individual needs, such as:
- Quality improvement & monitoring
- Industry 4.0
- Process engineering
- Energy saving
- Cost reduction
- Operator friendliness
- Performance increase
- Occupational safety
CHOOSE FROM DIFFERENT RETROFIT SOLUTIONS FOR YOUR CONVERTING MACHINE
Inline FLEXA II (printer)
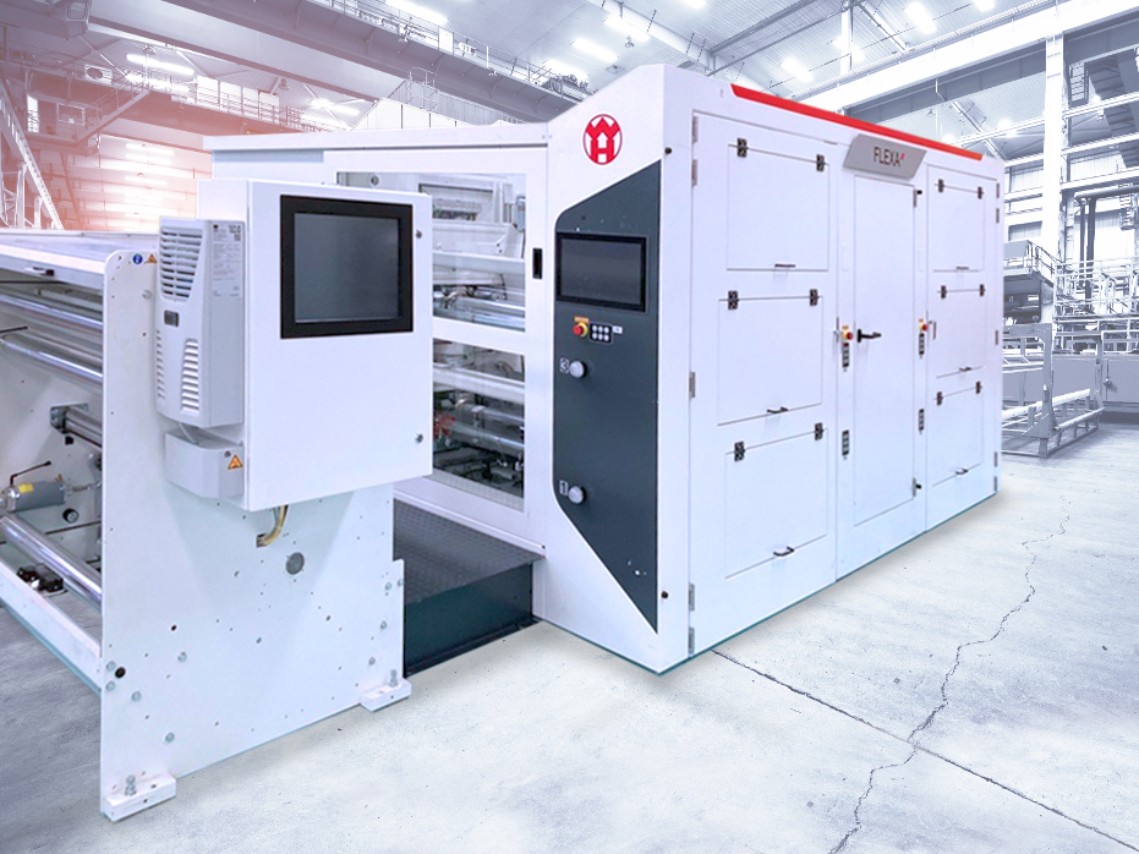
INSTALLATION
Approx. 10 days
Pre make ready „Eco Plus“ (printer)
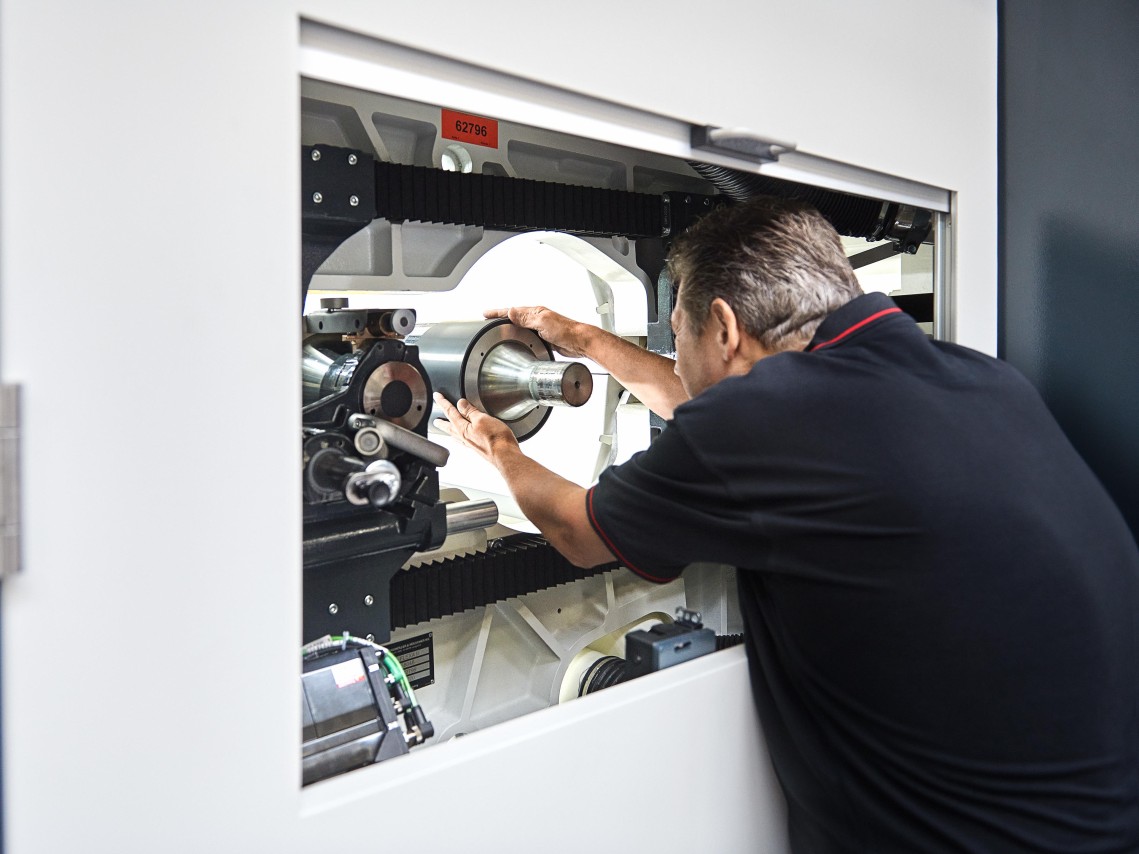
INSTALLATION
Approx. 4 days
Sleeve Technology „Eco“ (printer)
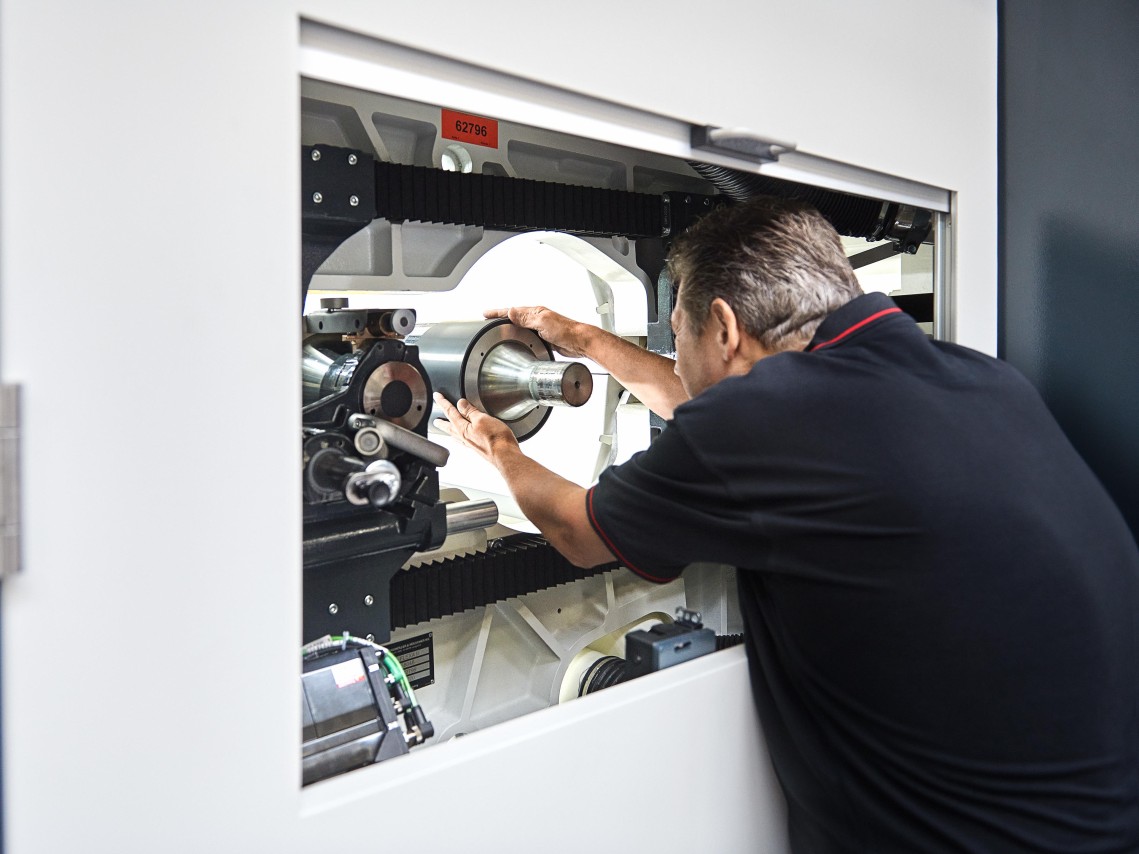
INSTALLATION
Approx. 3 days
Enclosed doctor blade chamber (printer)
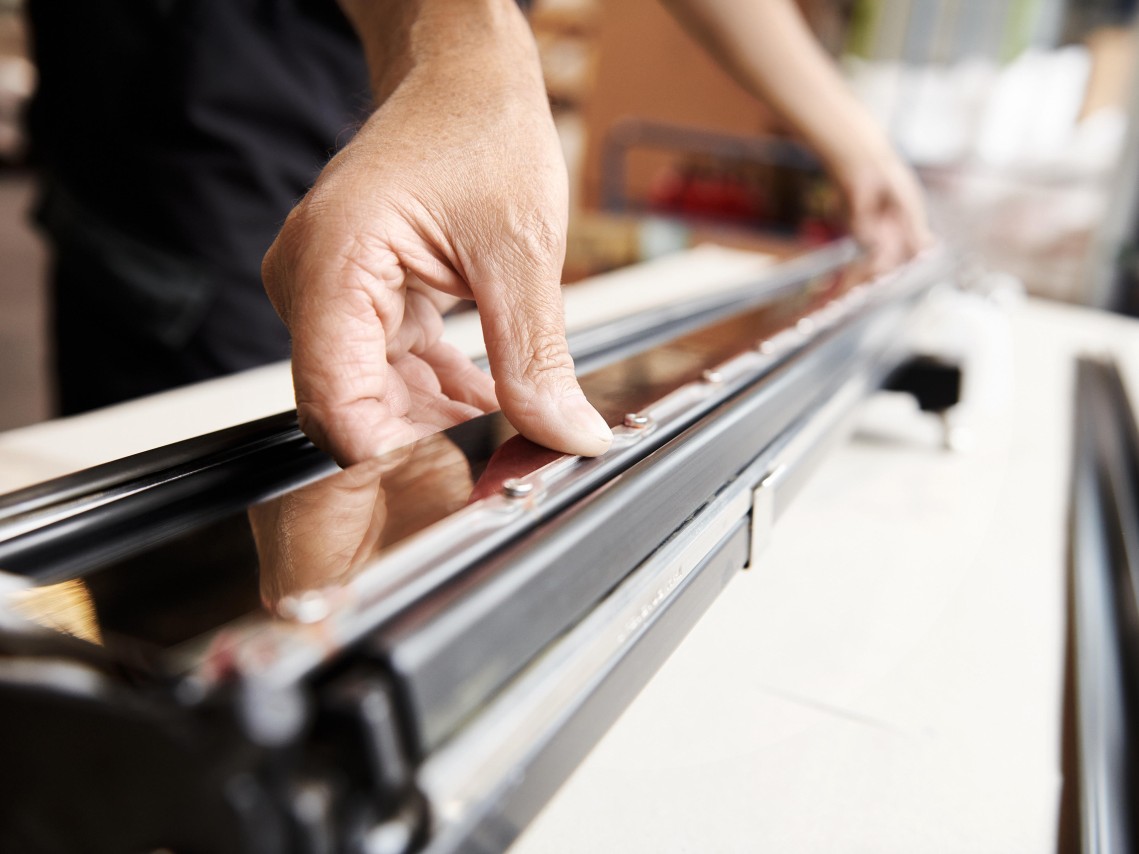
INSTALLATION
Approx. 1 day
Fountain roller to doctor blade chamber (printer)
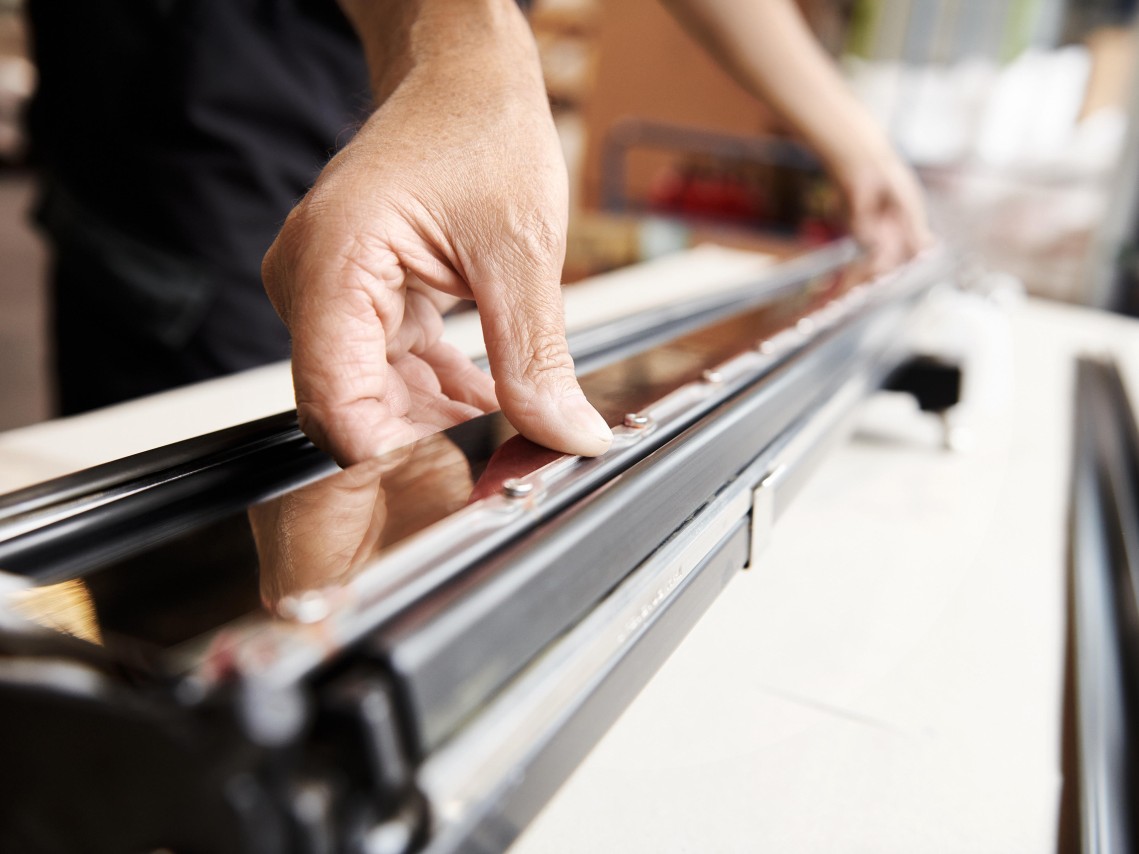
INSTALLATION
Approx. 4 days
Non-stop Roll Change (tuber)
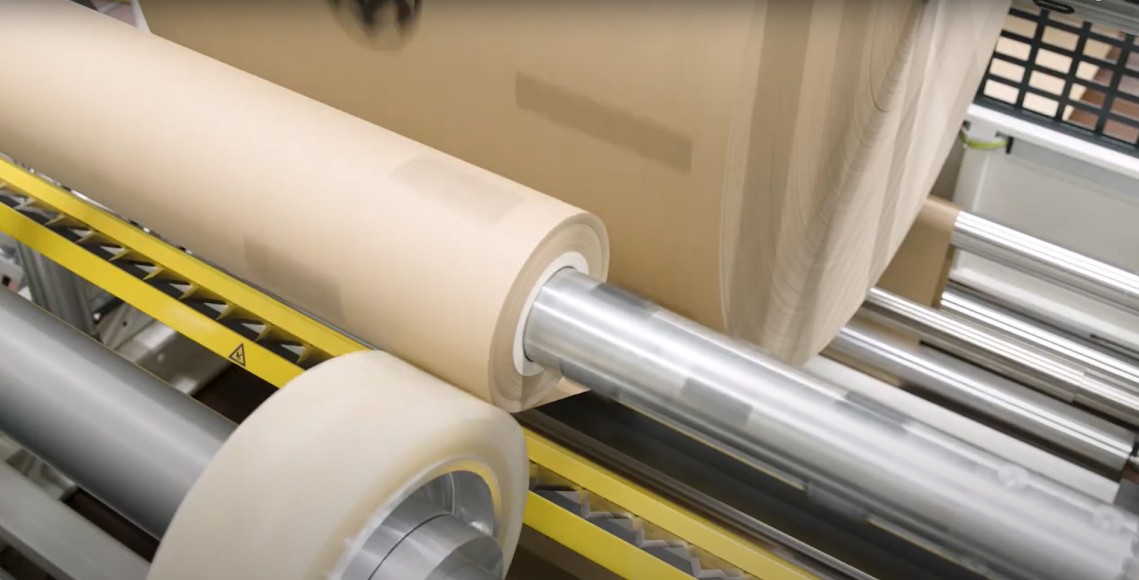
INSTALLATION
Approx. 4 days per unit
Venthole Perforation (tuber)
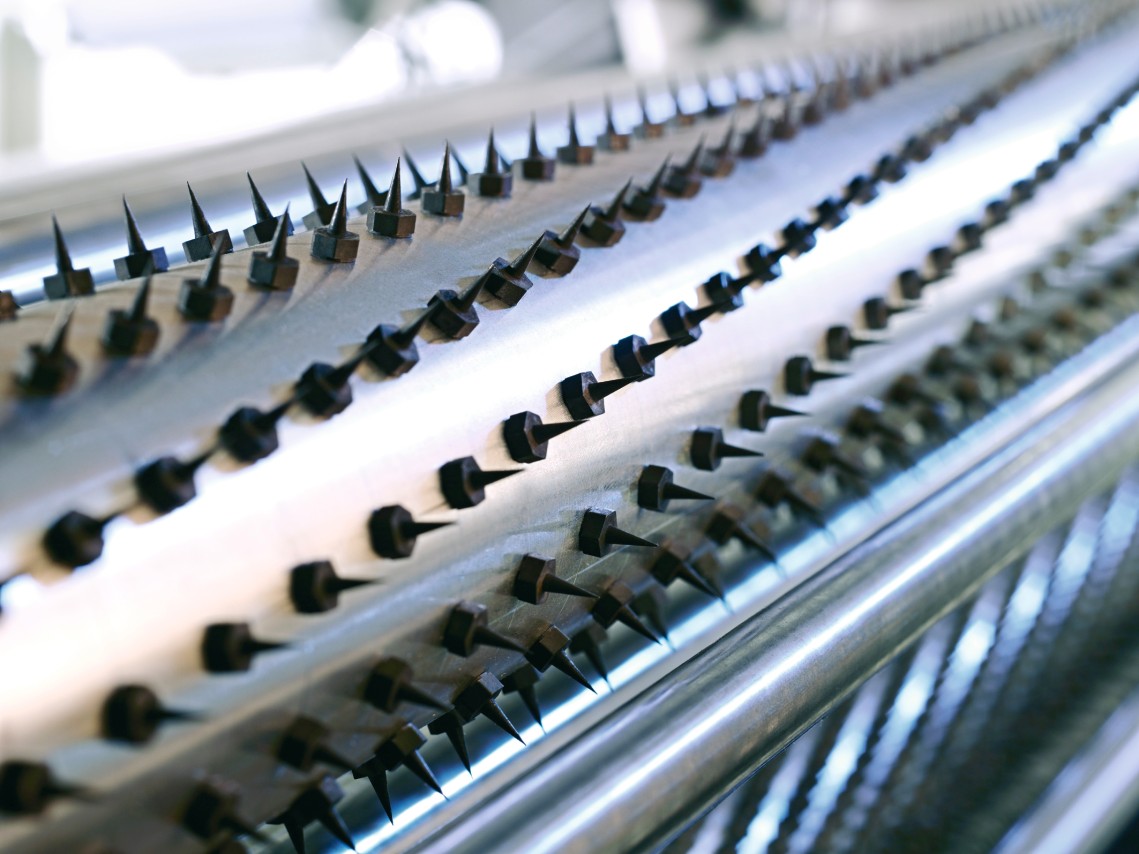
INSTALLATION
Approx. 2-3 days
Carrying Handle Unit (bottomer)
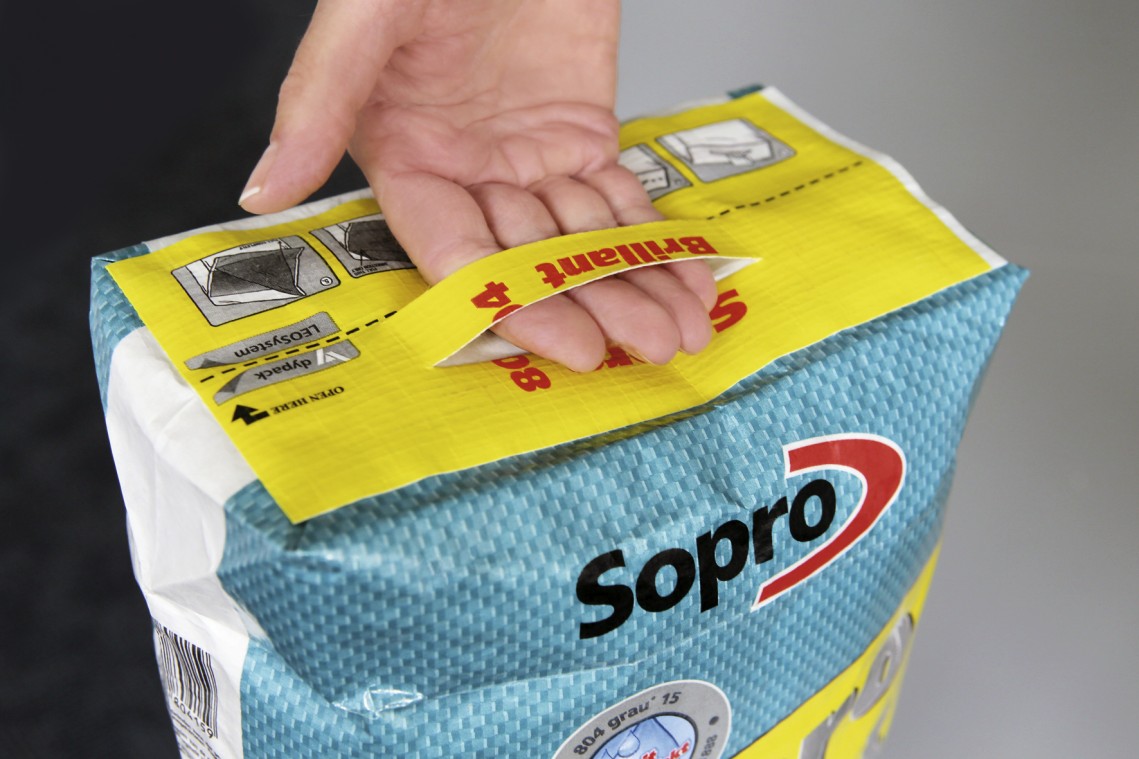
INSTALLATION
Approx. 1 day per unit
Easy Opening (bottomer)
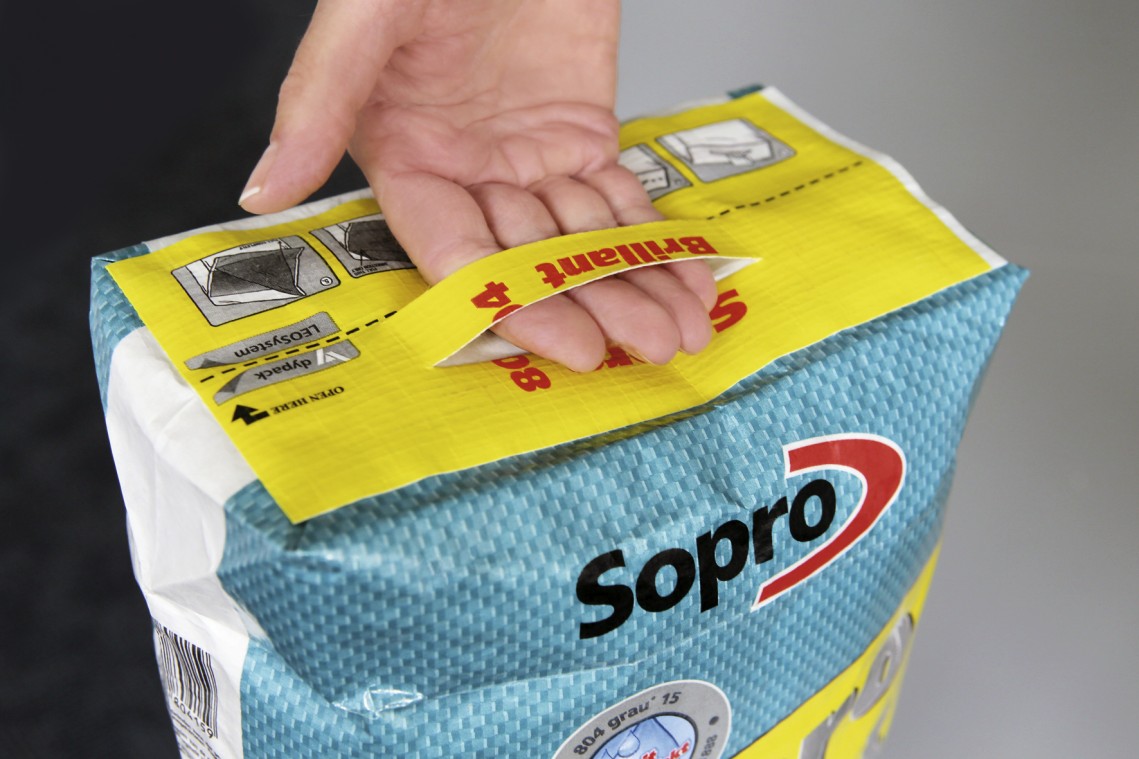
INSTALLATION
Approx. 1 day per unit