Tipografic - A true story of positive growth
... or how they went from "...riding a BMX to riding a 29” race bike!”
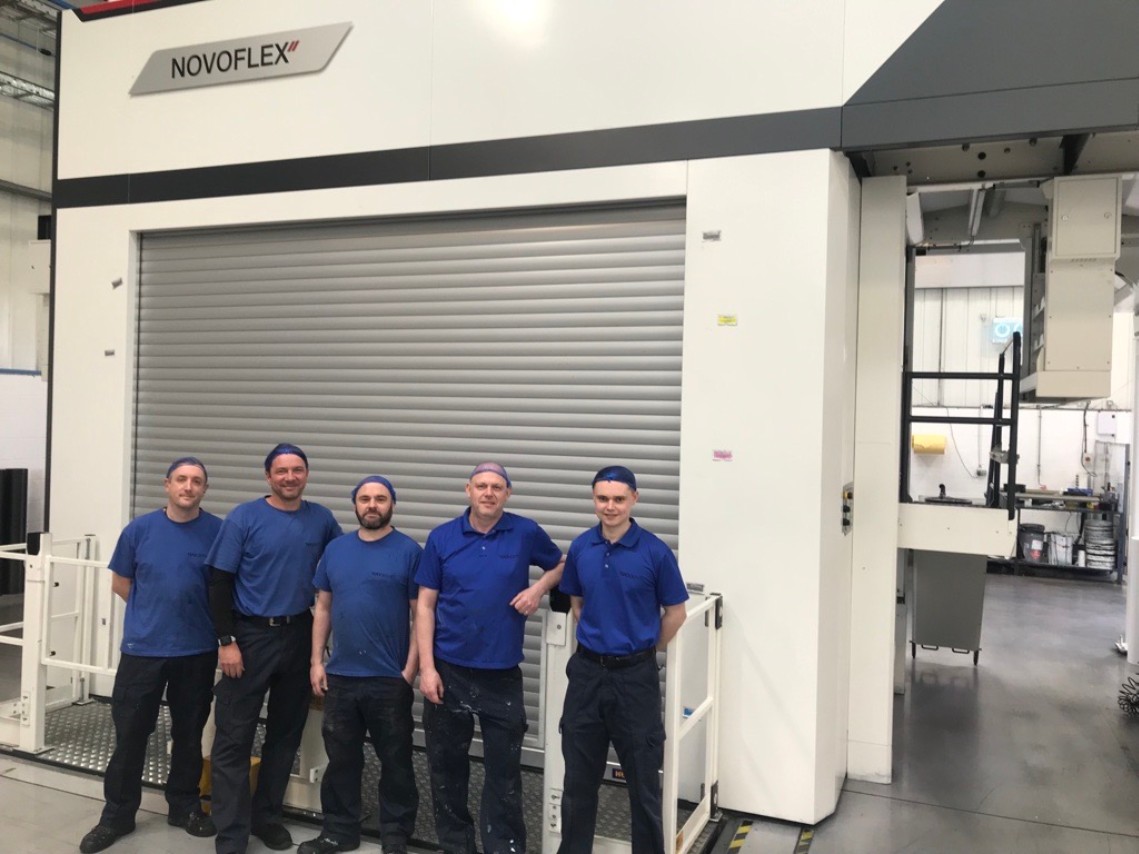
Evolution: From litho to flexo print
Tipografic started life 33 years ago and initially offered offset sheet fed printing techniques for B1 colour charts and gradually took in work for B2 labels for small runs, which was basically work that other printers didn’t want to do. Tipografic’s focus was on service and quality. As Litho work grew, the site moved from Bromborough on the Wirral to a purposely built facility at Morpeth Wharf in Birkenhead near Liverpool, which included the installation of larger Litho machines.
Customers started transitioning from paper to plastic around 17 years ago and an idea to move onwards from the three Litho machines to reel to reel flexographic printing came about. Customers wanted Tipografic to supply them with both paper and plastic label options. This was all about diversifying the business into different markets. With much deliberation and after thorough investigation and in-depth evaluations of many flexographic print machine manufacturers, an easy decision was made to partner with W&H. W&H was seen as the ideal partner in terms of the standard of equipment, knowledge and support to start up a new section of the business with relative ease.
New markets, new business
So, nearly nine years ago in 2013, the decision was made to fulfill this transition. This of course meant that Tipografic could hit the ground running with unrivaled quality and efficiency. With the machine installation taking place in 2014 a competitive edge was gained by Tipografic in the market. It really was a decisive partnership that changed the dynamics of Tipografic’s business.
Tipografic have a real admiration for W&H’s build quality, reliability and service, along with the attribute of W&H’s remote service capabilities. The Remote Service system that W&H offer for 24/7 support has been particularly useful to Tipografic, especially in the early days of production when support was needed and appreciated.
The first MIRAFLEX AM 8 was a great success with its ease of use and long-term reliability. However, the further investment for a MIRAFLEX II AM in 2017 proved a game changer and a huge step forward with the revised machine design and the incorporation of the newly developed VISION System . The VISION System allows the operator complete control for all areas of the functioning machine from one control point.
Moving up a gear
After the successful MIRAFLEX installations and with the business in a great position, a decision was made to move up a gear. The decision was made in late 2018 to make another investment and the brief was to go with the new NOVOFLEX II. With it, Tipographic wanted to take care of very demanding print designs that were being asked for in the market and to optimize these designs with much higher throughput. The MIRAFLEX´s could then be utilized for small print runs and thus added to the extra efficiency of the overall production scenario.
At present the NOVOFLEX II primary task is long run production and can top the MIRAFLEX ´s throughput by as much as 50%. This also means that the factory only has to work a five day week schedule which is handled with ease. The NOVOFLEX II was installed during the height of the Covid pandemic, with most of the commissioning done remotely. It was not an easy process, but with a little more time than usual a successful installation was achieved.
Tipografic have absolutely no hesitation to recommend W&H to any potential customers and are proud to be their partner. They fully agree with the W&H slogan PASSION FOR INNOVATION.
The NOVOFLEX II has opened Tipografic’s minds and a particular comment was made that “the business has gone from riding a BMX bike to riding a 29” race bike!”