Efficient Production of Barrier Films with the Right Technology
High-quality barrier films are used worldwide to protect food and other sensitive goods. Global demand is growing, while at the same time the demands on performance features and sustainability of the packaging solution are increasing. Andreas Hoppe, an expert for barrier applications at W&H, explains which technology is most efficient when and why the first customers are using 11-layer lines for blown film .
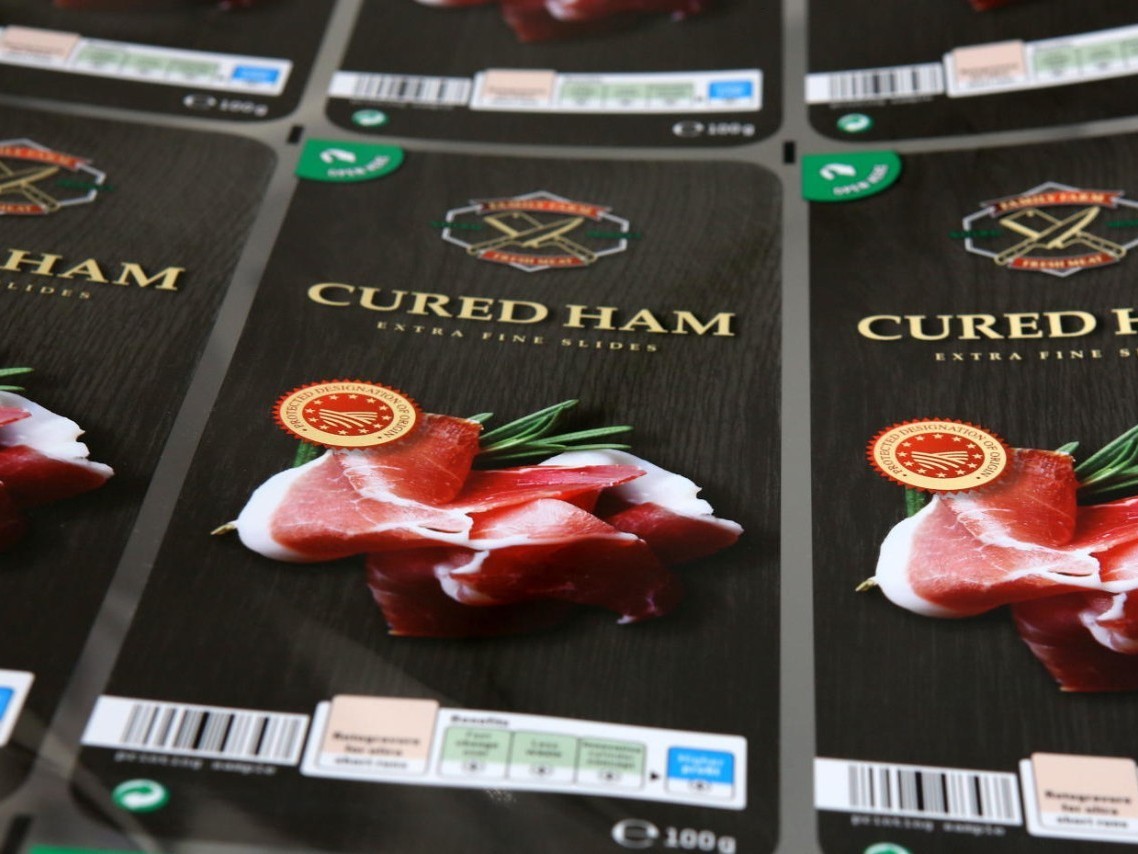
When selecting the right technology for barrier film production, film producers have the choice between blown film and cast film technology. Which process is more efficient depends on the final application and the required film properties. Film thickness, height of the gas barrier, film strength and sealability play a role. Cast film lines with higher output are particularly economical for large batch sizes. Especially thicker films with high transparency can be optimally produced as cast films thanks to efficient cooling, for example for deep drawing applications. If different formats and thicknesses are required, e.g. for lid films, the blown film scores with flexibility due to fast format changes. Due to the lower cooling and the resulting higher crystallinity, applications with higher stiffness can also be produced.
7- and 9-Layer Lines are Standard, 11-Layer is the Next Step into the Future
Cast film lines with 11- and more layers have already been in operation for some time. There is also a trend towards multilayer systems for blown film. "7- and 9-layer blown film lines are now standard in barrier film production. Today, they can be used to produce the entire spectrum of food films," explains Hoppe. The first 11-layer system for barrier applications from W&H has just been sold in Asia. "Long-term flexibility is an important purchasing criterion, especially for barrier films. More and more new recipes are being developed in response to increasing demands for function and economy. With 11 shifts, the customer is certain that he can continue to run high-quality films with the most modern recipes in the future, and that profitably," says Hoppe.
More about barrier films
Barrier films use a gas barrier to protect goods from environmental influences such as oxygen and moisture. They are used for products sensitive to moisture or oxygen or products with intensive odours. Typical areas of application are e.g. cheese and sausage packaging. The demand for high-quality barrier films is growing worldwide, for example to secure food supplies in growth regions.
A distinction is made between barrier films (PE + polyamide) and high barrier films (PE + polyamide + EVOH). Symmetrical formulations are characterized by the fact that the outer and inner layers come from the same family of raw materials, with the barrier layer as the middle section. Asymmetrical formulations, on the other hand, have two different families of raw materials in the inner and outer layers.
Important criteria for the production of barrier films:
- Consistent film thickness for optimum further processing
- Individual layer thickness tolerance for efficient use of resources
W&H machines for the extrusion of barrier films:
- VAREX II: The blown film line for optimum combination of quality, efficiency and flexibility
- AQUAREX: The water-cooled blown film line for applications with high demands on optics, puncture resistance and deep-drawability
- FILMEX II: The cast film line for highest quality and output of barrier films
W&H machines for printing barrier films
- HELIOSTAR II - The gravure printing machine for demanding motifs, e.g. in the halftone range and with the finest gradients, fonts and structures
- DYNASTAR - The gravure printing machine for highest print quality and high efficiency even for short jobs
- MIRAFLEX II: The flexo printing machine for optimum quality at high speeds, also for the use of water-based inks
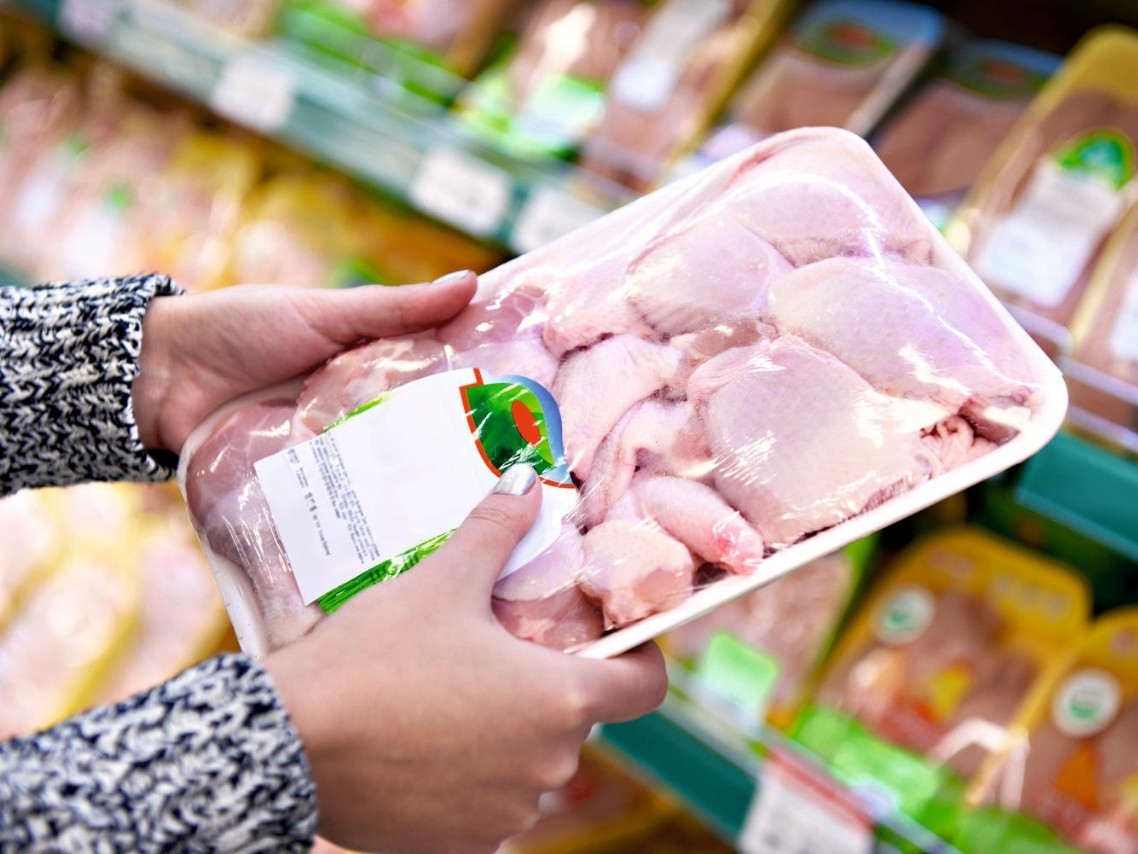
New approaches to the sustainability of barrier films
Sustainability is currently a major driver for new formulations, for example. Barrier films make an important contribution by reducing food losses and enabling hygienic packaging. One challenge that raw material manufacturers and producers are working on is their recyclability. "For example, there are developments in water-soluble and biodegradable barrier materials. Today, these materials are not yet available in large quantities and more expensive than standard materials. This makes it all the more important that the raw materials are used optimally," explains Hoppe.
W&H blown film lines for barrier films: efficiency and quality
W&H blown film lines are used worldwide for the production of high-quality barrier films. "We have over 200 barrier film production lines on the market," says Hoppe. W&H blown film lines are particularly efficient and flexible. The MAXICONE die head with patented conical distribution system enables the implementation of a wide variety of structures, even with extreme layer ratios. The universal W&H HPS barrier screw guarantees flexibility in processing a wide variety of raw materials, such as PE, PP, PA and EVOH. Expensive raw materials can be run very thinly due to very good individual layer tolerances. Short flow paths in combination with small amounts of material in the tool prevent material degradation of sensitive raw materials and enable fast material changes.
Everything from a single source - from extrusion to printing
In addition to the lines optimized for barrier films, W&H's consulting expertise with decades of market expertise is an important success factor. "W&H is the only machine manufacturer to offer air-cooled and water-cooled blown film lines as well as cast film lines in one portfolio. This enables us to provide independent technical consulting. We have the right system in our portfolio for every application," explains Hoppe. W&H also offers both gravure and flexo printing systems for the subsequent printing of the barrier films. "Thanks to our knowledge of the entire process from extrusion to processing, we can provide better advice on, for example, which tolerances in film production ensure optimum further processing in printing. We support our customers in achieving the optimum overall result for their barrier film packaging solution", Hoppe sums up the range of services.